Как и обещал, я съездил в Ригу, чтобы посмотреть, что и как делается на производстве акустики Arslab. На фабрике показывали всё, без каких-либо оговорок или ограничений, не было ни одного места, куда нельзя было пройти и сфотографировать. Одно-единственное маленькое ограничение за весь визит — не снимать кое-что из новых композитных материалов, и то только крупным планом, а остальное все можно рассмотреть вполне подробно и в деталях.
Производство у Arslab небольшое: несколько цехов, плюс склады материалов и готовой продукции. Здесь не делают десятки тысяч пар акустики в год, цифры скромнее, но несколько тысяч экземпляров все же уверенно набирается. Сотрудников — около 20 человек. Организован процесс работы обстоятельно, здесь мало «поточки» и автоматизации, а есть внимательное отношение к материалам и процессу.
На этой рижской фабрике изготавливают все линейки Arslab и Old School, сюда же перенесена сборка акустики Penaudio (разработка по-прежнему в Финляндии, у основателя компании Сами Пенттила). Кроме того, понемногу делаются проекты для сторонних производителей — например, кое-где я увидел заготовки для одной итальянской компании, совсем дорогой и хайэндной. Но сторонние производители нас сейчас не очень интересуют, а обо всем остальном надо рассказать по порядку.
Я сосредоточусь именно на производстве, потому как о процессе разработки Arslab и Old School вы можете почитать в интервью главного конструктора компании Юрия Фомина, а о самих брендах и бизнесе — в интервью Артема Фаермарка, главы «Аудиомании», которой так или иначе принадлежат эти бренды и само производство.

На производство же посмотрим именно как на технологическую цепочку, которую нам представил Виктор Лагарпов — технический директор компании. Когда все спроектировано — дальнейшее начинается с корпуса, а корпус начинается с материала и его нарезки. Оговорюсь, что именно разработки акустики здесь нет (разработка Arslab и Old School — в Москве, Penaudio — в Финляндии), но после макетирования и первых стадий прототипы корпусов делают именно здесь, а собственное производство упрощает задачу.
На практике же все начинается с подбора материалов (и не всегда только МДФ и аналогов, но про используемые сэндвичи я рассказать не могу — секрет) и с вот такого станка, который по заданной программе нарезает заготовки нужного размера и формы.

Дальше, логично, что все оклеивается шпоном. Или не оклеивается, если предполагается лаковая отделка. Кстати, шпон на производстве подбирают, подготавливают, но для самой склейки отвозят на предприятие по соседству — слишком специфический процесс, отличающийся от общей цепочки и требующий других условий. Хотя сам исходный шпон разный. Все-таки вариантов отделки у производителя не так уж и мало.
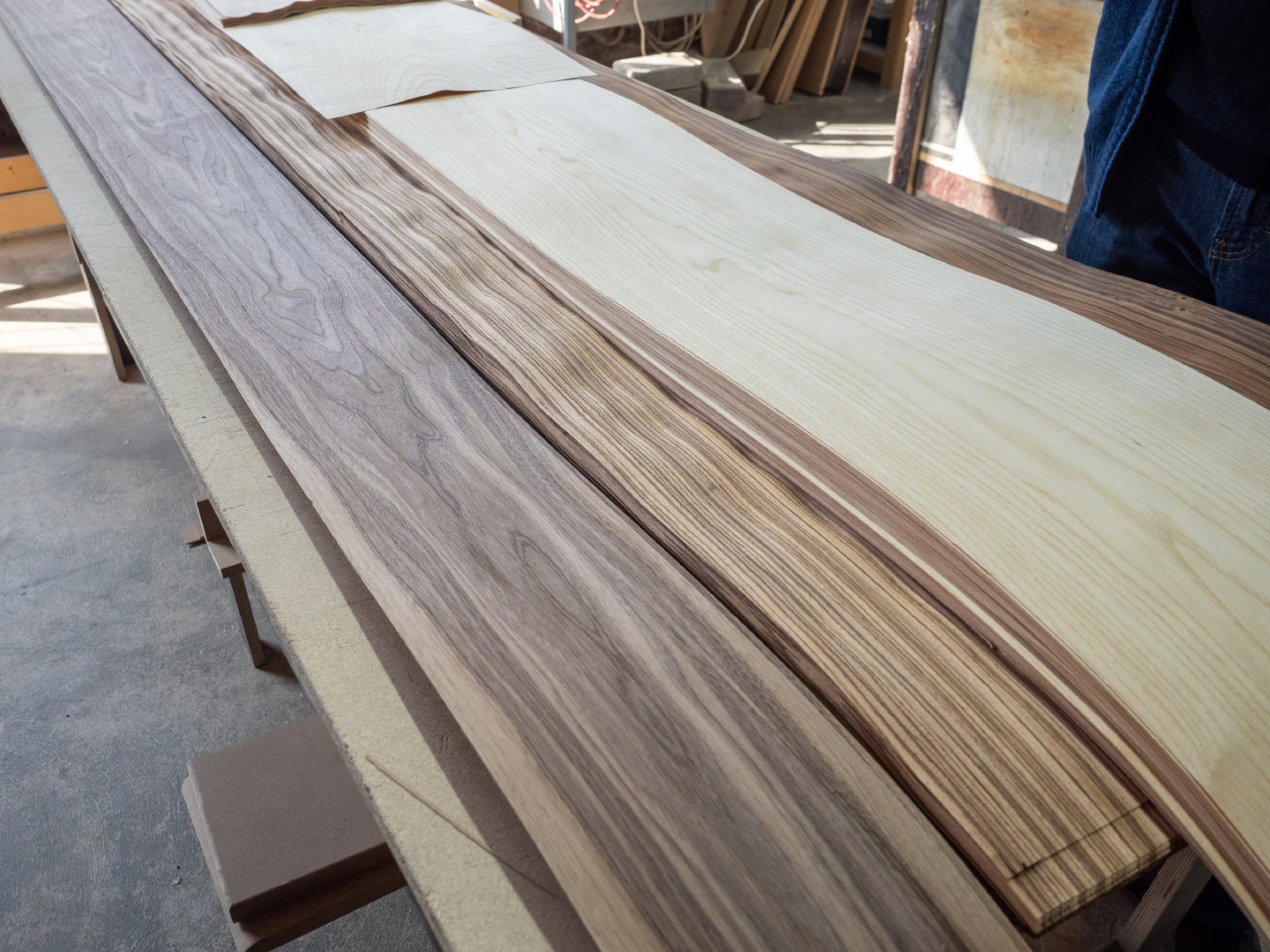
Есть и весьма дорогостоящие виды шпона: например, знакомая по некоторым моделям карельская береза — так она выглядит в виде заготовки.
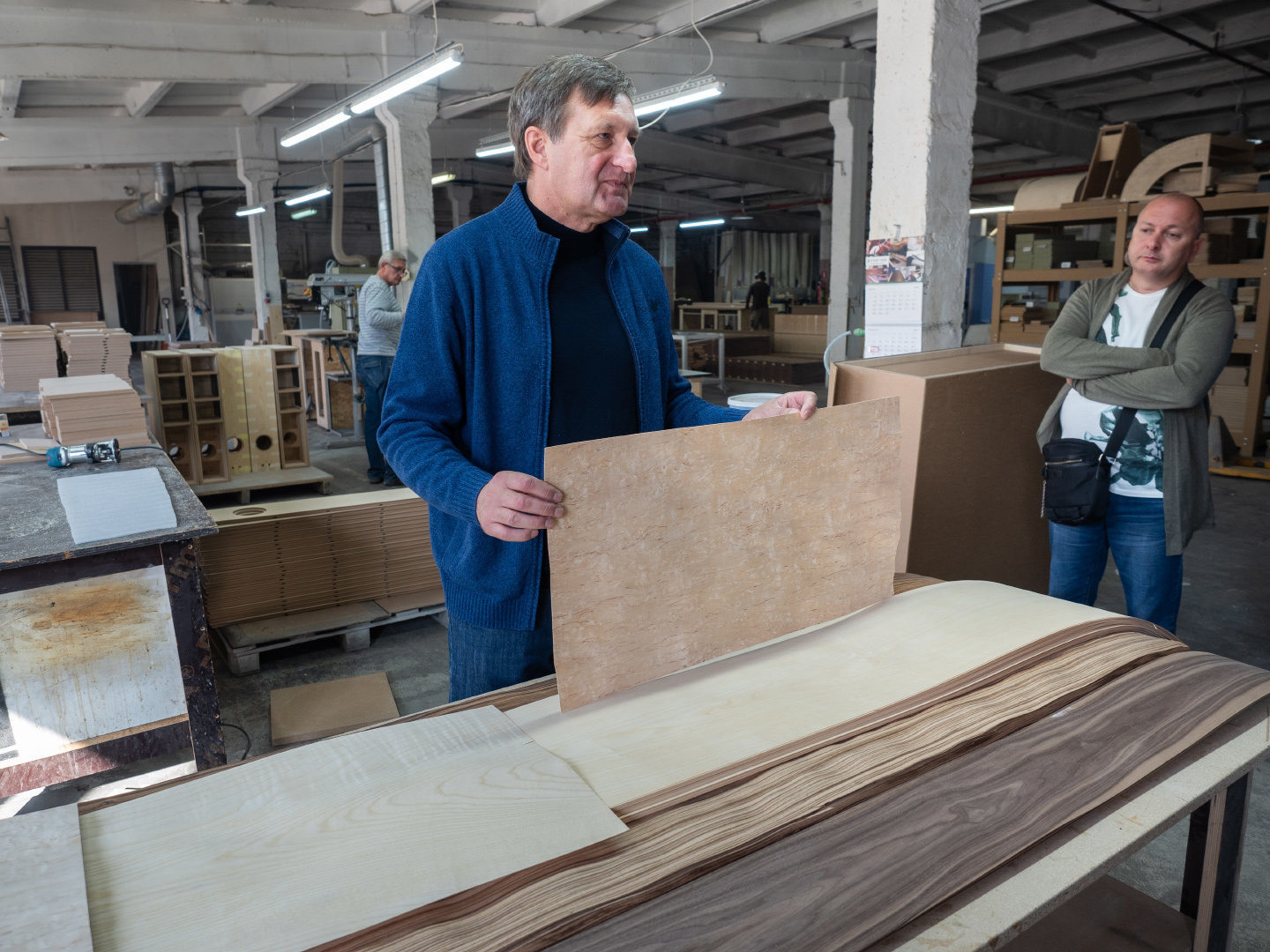
После склейки получаются вот такие заготовки. Все аккуратно и, надо сказать, качественно — сам шпон и качество его укладки на уровне. Никаких пузырей, трещин или шпатлевки я не увидел.
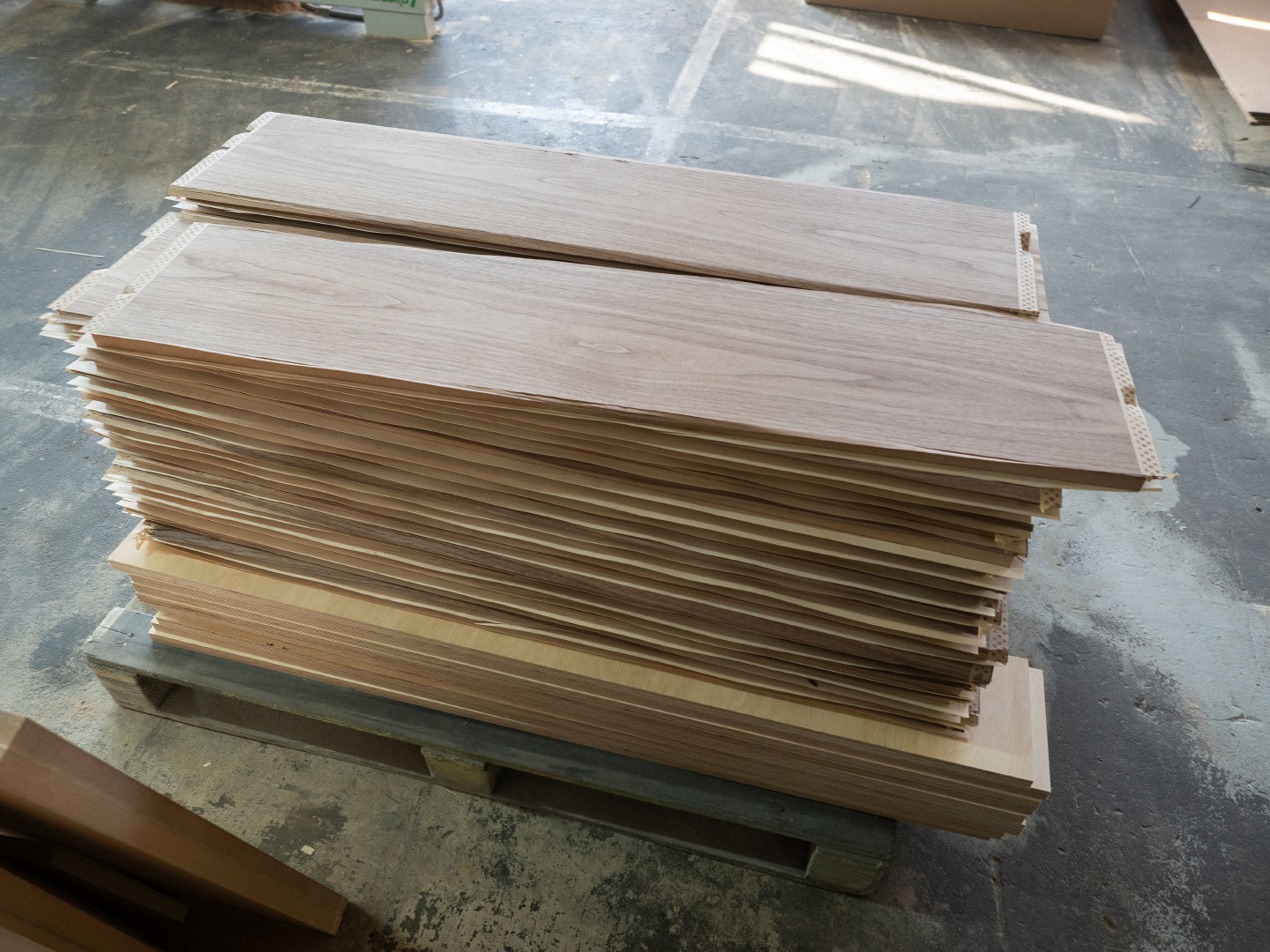
Кроме шпона в ряде моделей используется фирменная отделка торцевыми спилами. Делают их из такого сырья, а не из обычной покупной фанеры, конечно же. Слои спилов «обычного» дерева склеиваются в массив, а массив, в свою очередь, нарезается на слои. Отделка получается немного непредсказуемой, но неповторимой и интересной.
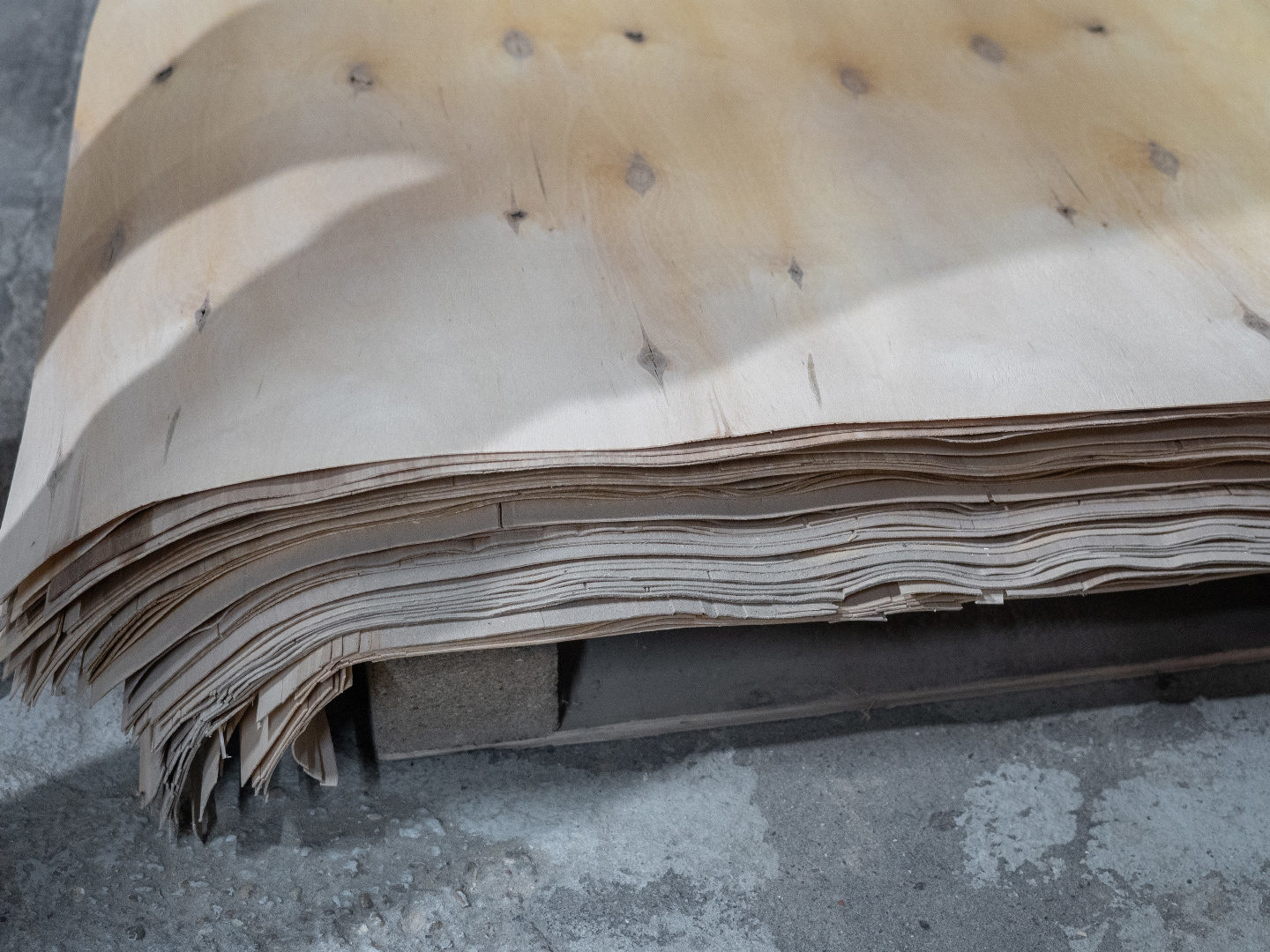
Конечно, слои спилов не могут быть такими же тонкими, как и обычный шпон — покрытие получится крайне хрупким и с ним будет невозможно работать. Поэтому толщина больше — на деле вот так выглядит это покрытие на заготовке будущей колонки.

Дальше абсолютно все заготовки попадают на следующий станок. Его задача — вырезать разом деталь, из которой будет собран весь корпус за исключением передней панели.
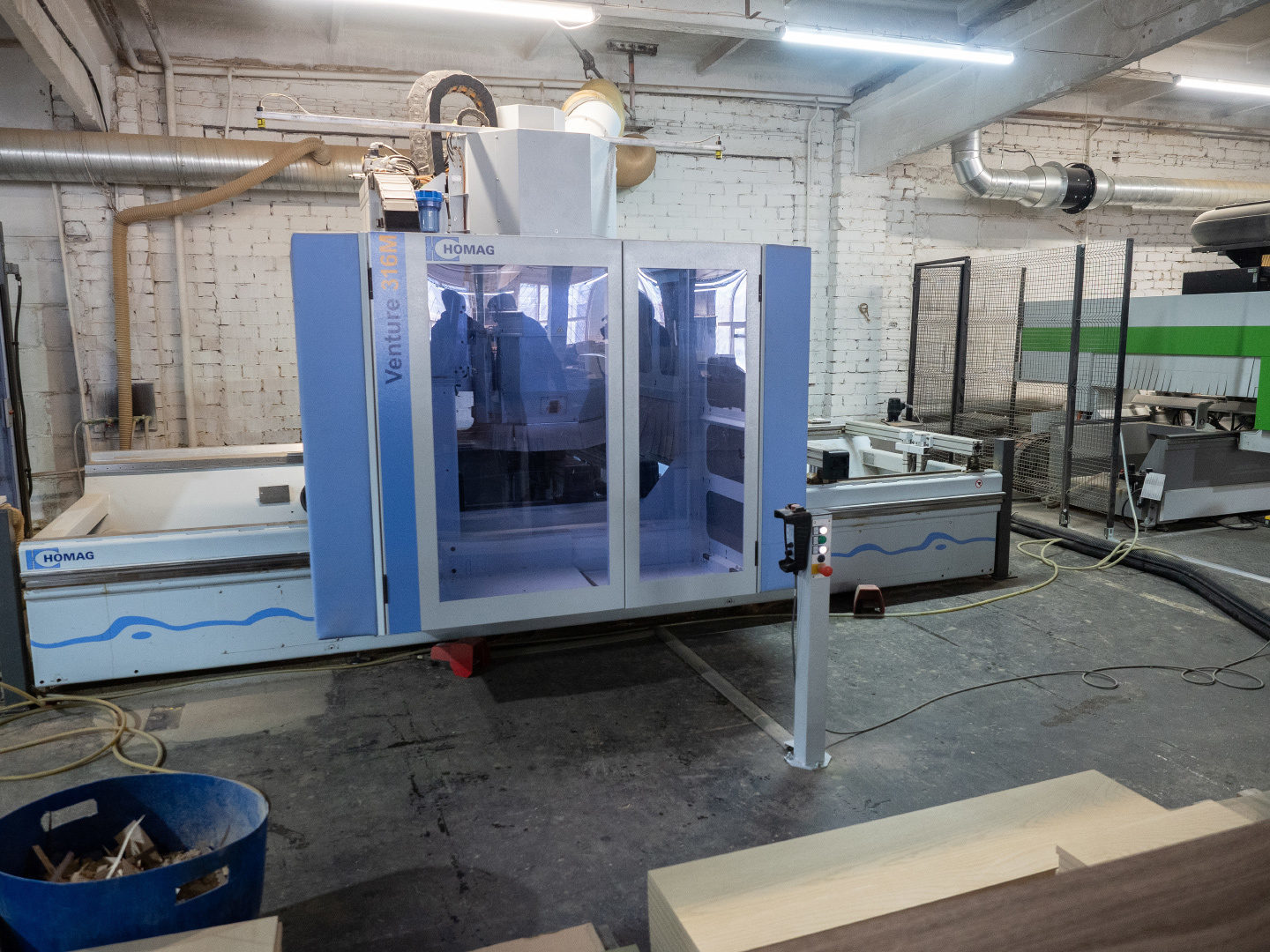
Казалось бы, не такая уж сверхзадача для станка с ЧПУ — «раскроить» по программе полосу шпонированного МДФ. Но на деле именно в этих углах, которые формирует станок, есть существенная специфика, определенная конструкцией корпуса.
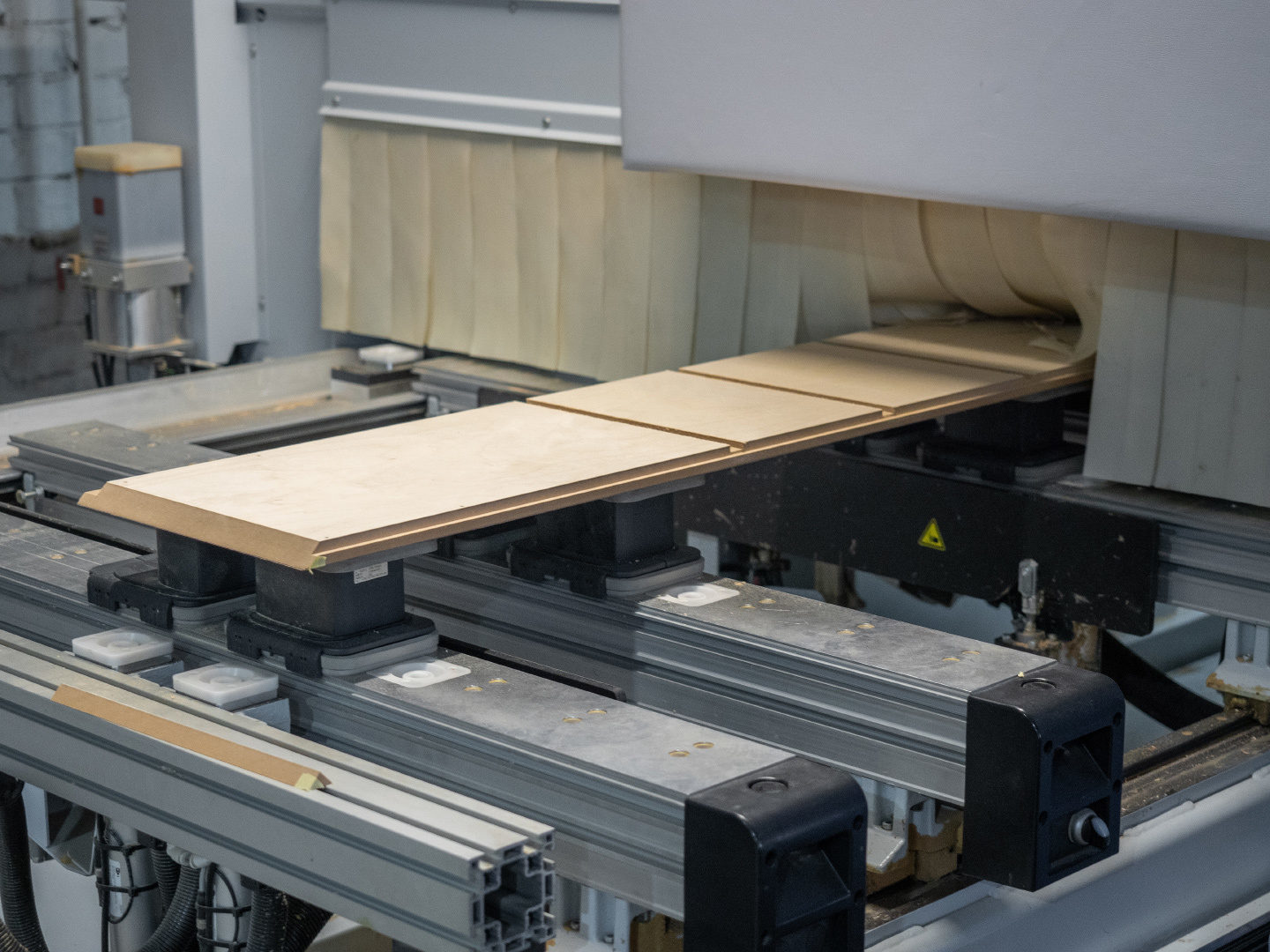
Углы под 45° нужно нарезать так, чтобы из них сложить 90°. Не очень сложно. А вот дальше интереснее: с внешней-то стороны деталь оклеена шпоном — насквозь его прорезать нельзя. Прорезать так, чтобы при изгибании он сломался — тоже.
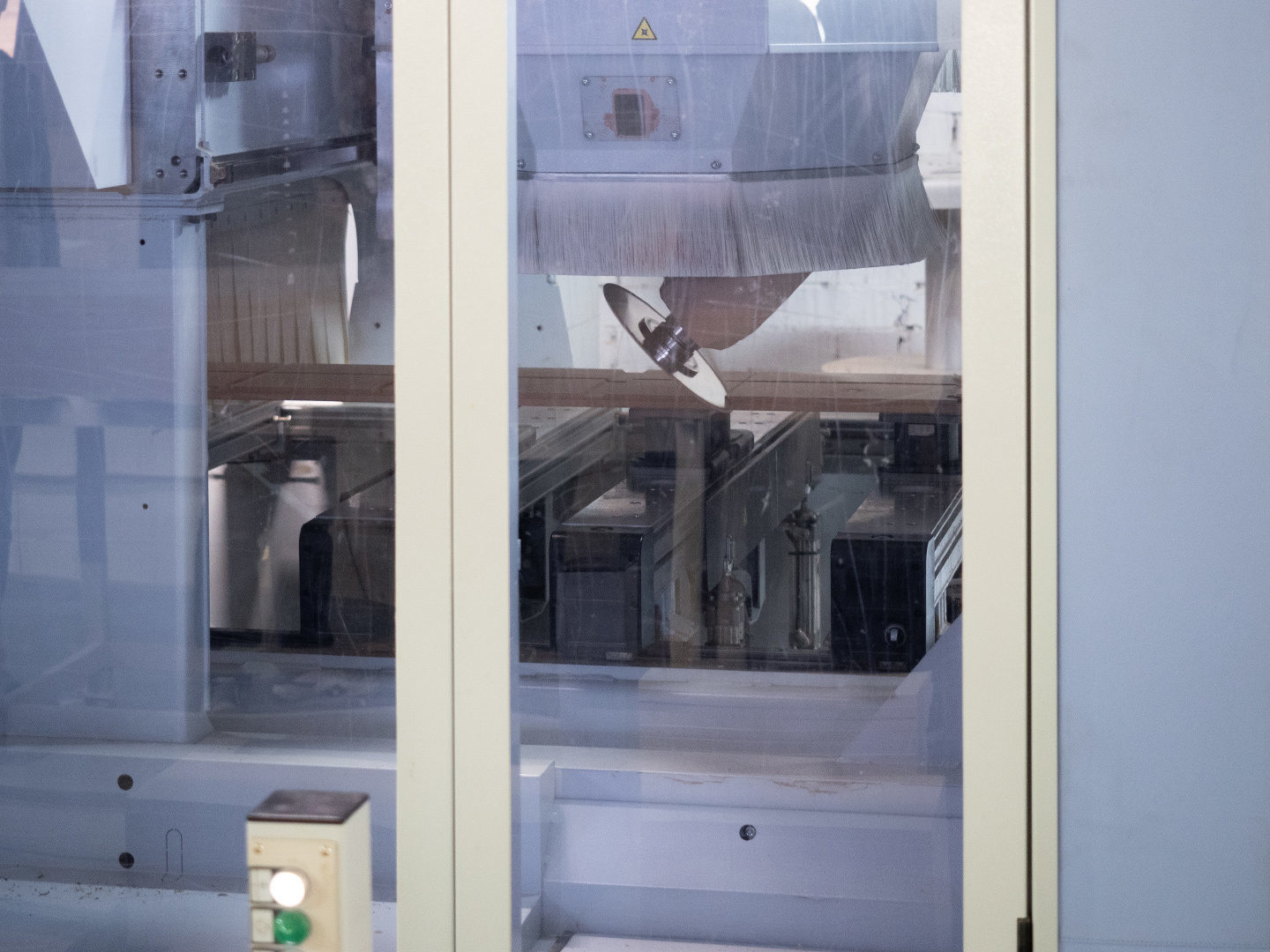
И очень необычно наблюдать, как рабочий, управляющий этой процедурой, складывает, как раскладушку, будущий корпус. Сначала все четыре стороны будущих боковых стенок лежат в одной плоскости и держатся только на тоненьком слое шпона, который, в свою очередь, тоже частично пропилен по толщине.
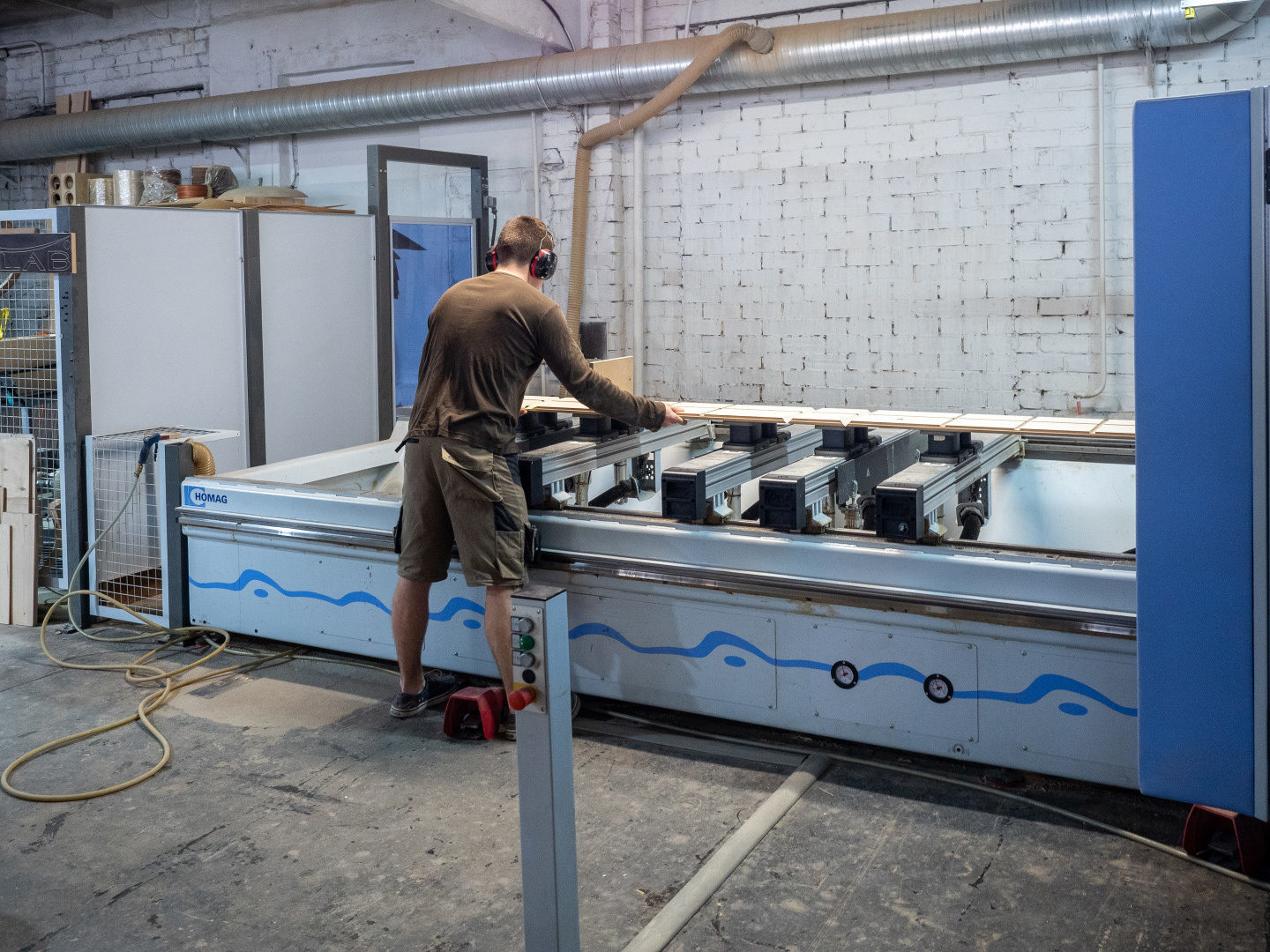
Несколько аккуратных движений — и уже вырисовывается будущая форма. Грани при этом подстраховывают только лишь бумажным малярным скотчем и поддерживающими переборками. На этом этапе сборки — никакого клея кроме того, что содержится на скотче.
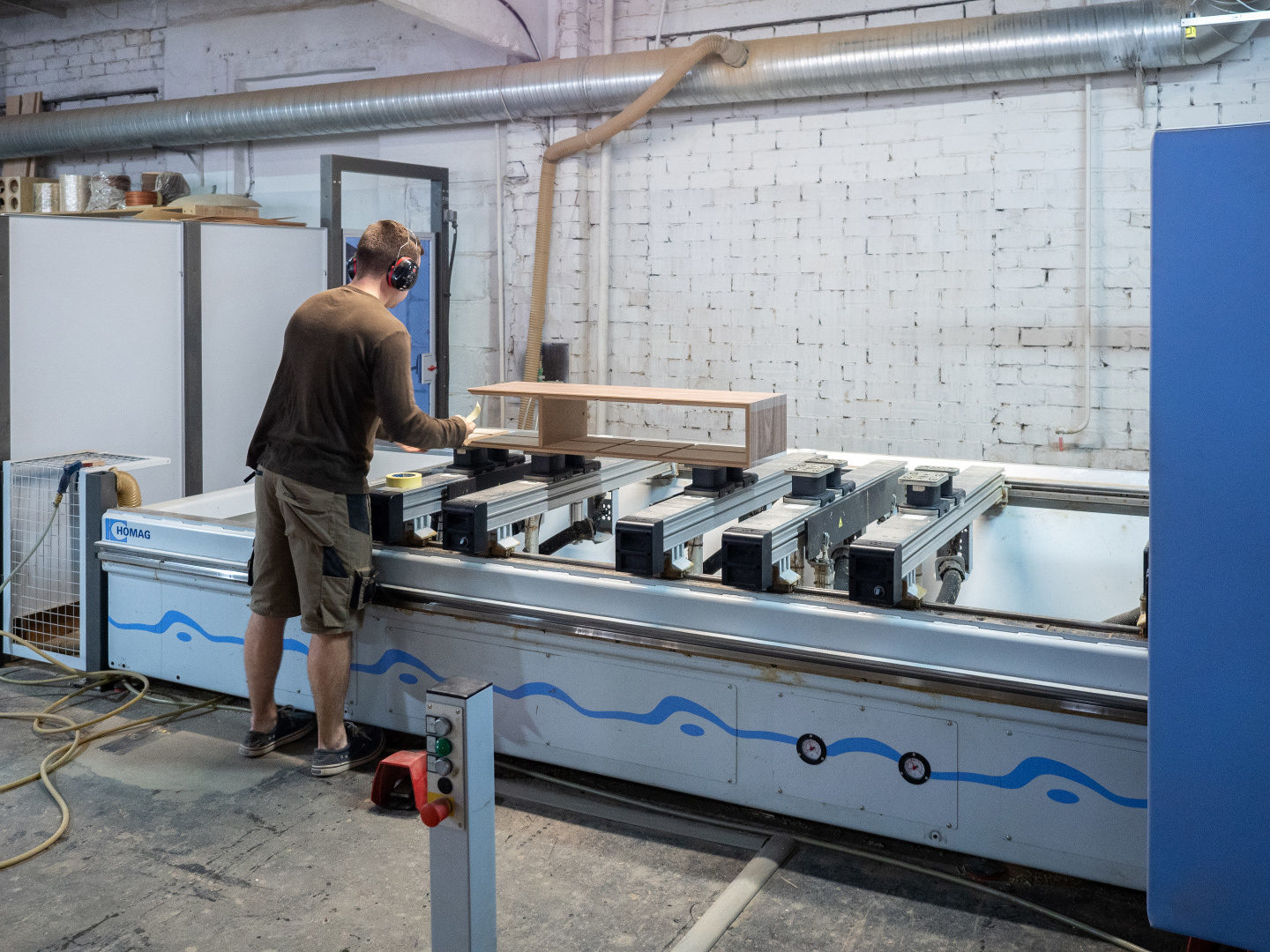
В результате получаются такие вот заготовки, ждущие следующего технологического этапа сборки.
Кстати, на заднем плане можно увидеть систему фильтрации воздуха. И дело не в экологических нормах — пыль, если ее не убирать, просачивается всюду, а это может негативно сказаться в дальнейшем. Кроме того, она влияет и на влажность, пусть даже на производстве имеются постоянно работающие системы активного увлажнения и контроля влажности. Ничем не защищенное дерево требует бережного обращения.

Параллельно работающая в этом же цеху линия делает все остальные плоскостные детали: передние и задние панели, основания. Тут все без особенностей — есть станок и есть результат его работы.
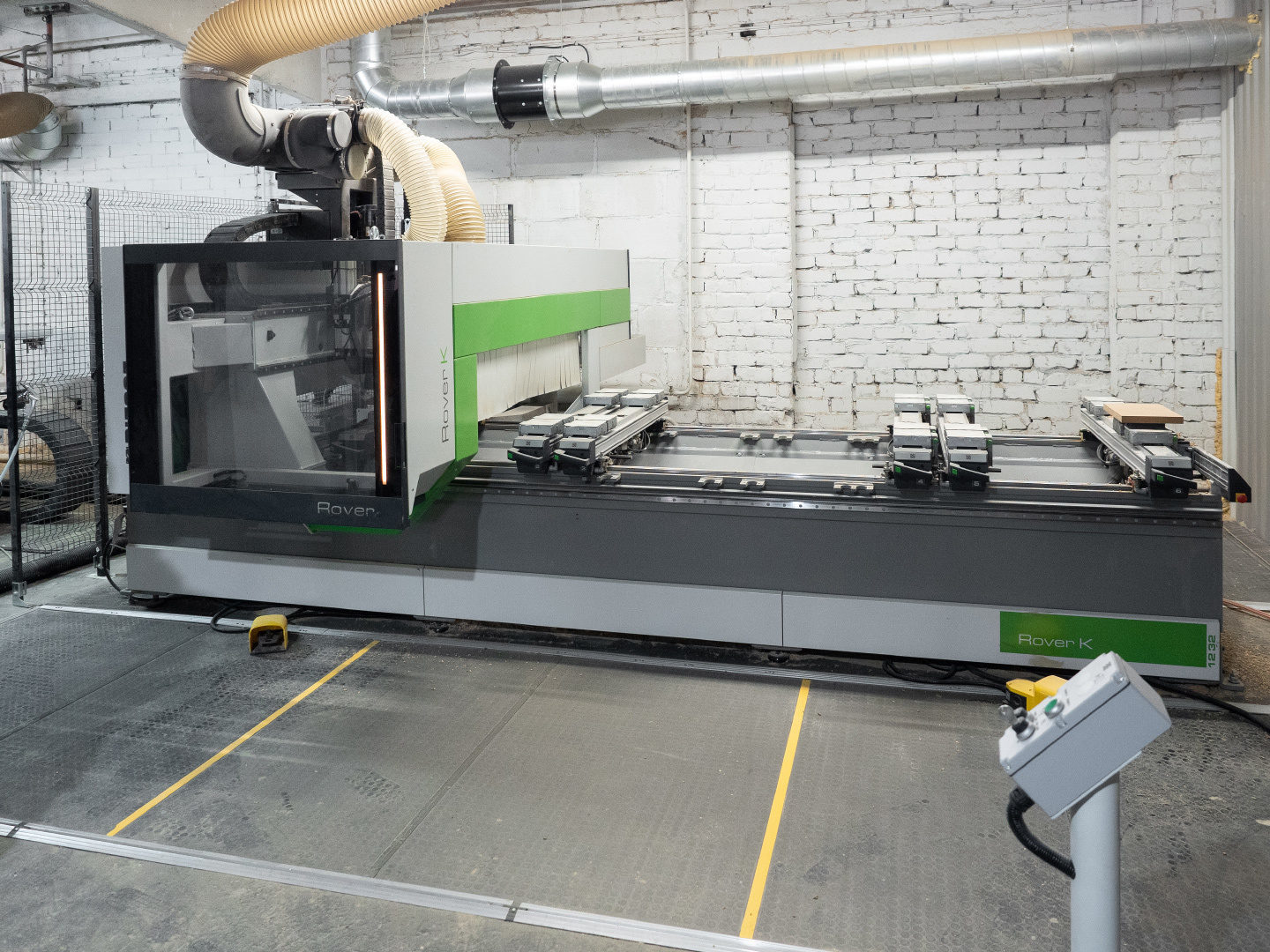
На выходе — все нужные для дальнейшей сборки корпусов детали, например, основания-подиумы. Сразу готовые, со всеми вырезами и технологическими отверстиями.
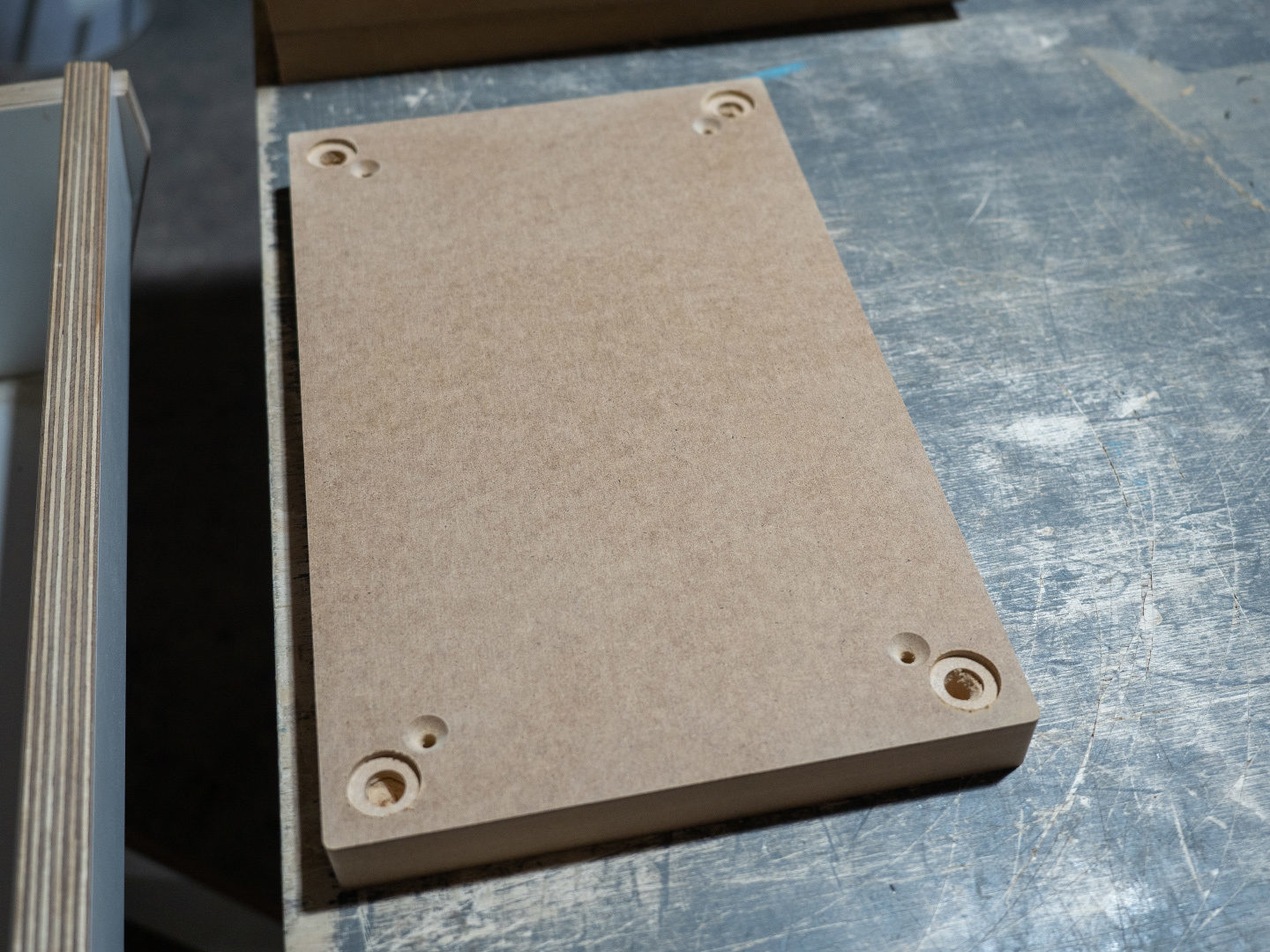
Или всевозможные передние панели.
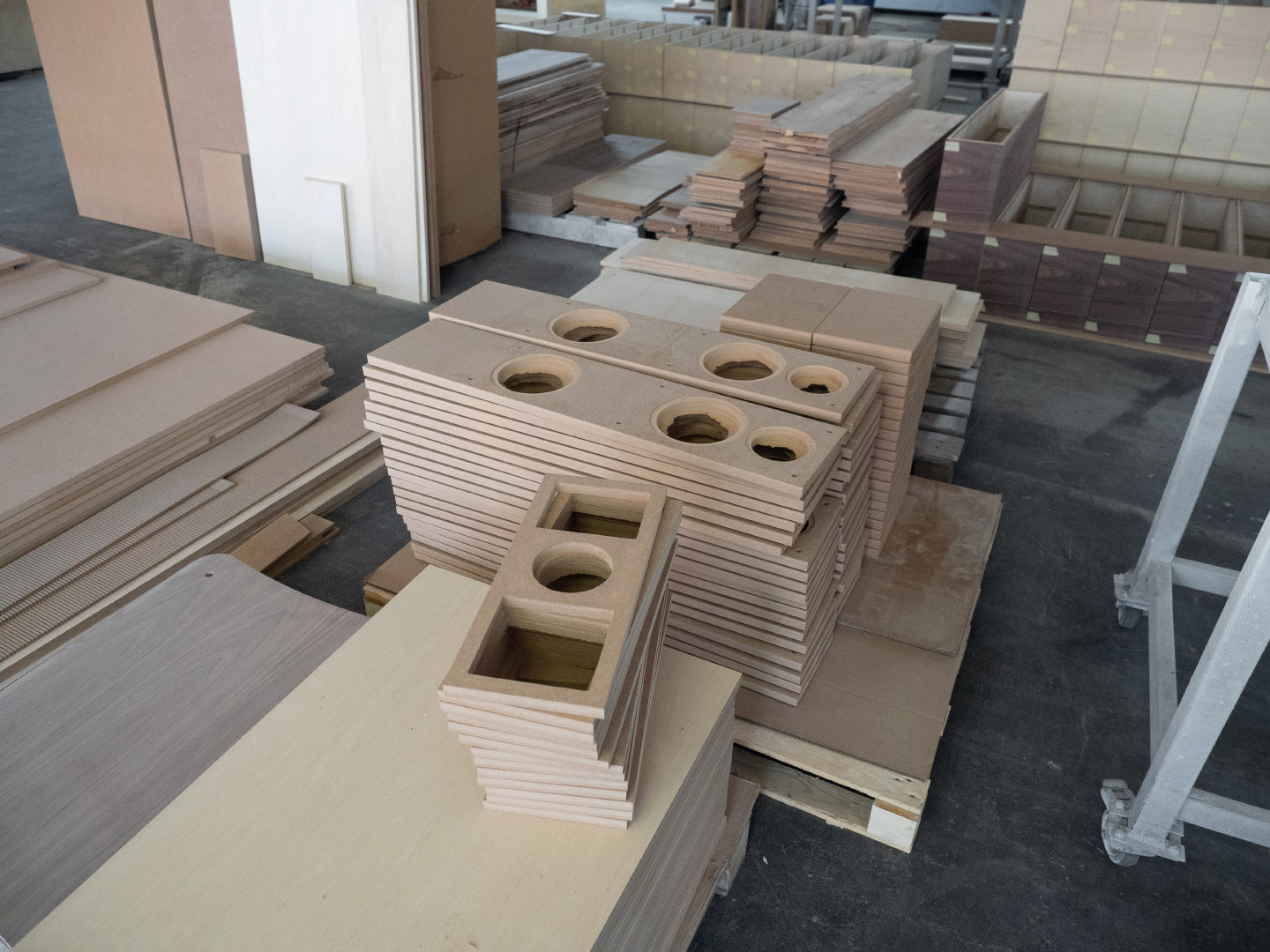
А вот тут вообще можно заметить много разного и интересного, кроме подиумов и панелей. Например, заготовки для подставок под акустику Cold Ray (и для акустических и аппаратных стоек все делается здесь же), а на верхней полке и вовсе заготовки для чего-то весьма крупного и рупорного, что как раз сделано по заказу для стороннего производителя.

А это «мозг» основных станков на производстве. Так что не лобзиком делают, и совсем даже не на коленке.
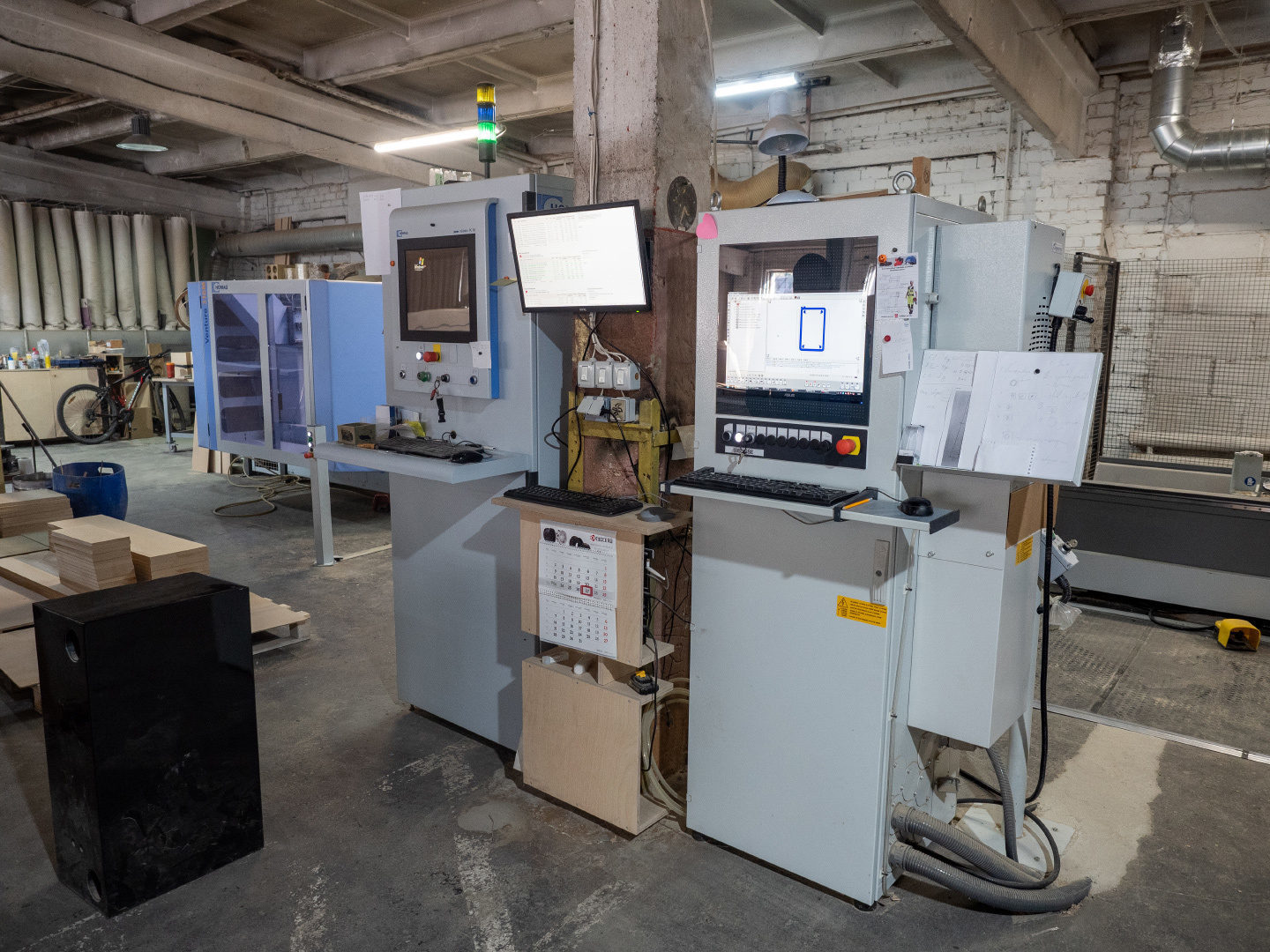
Дальнейшая же сборка как раз наоборот — полностью вручную, аккуратно и тщательно. Конвейерного производства здесь нет, но если посмотреть на скорость и слаженность работы и пересчитать на дни и часы, то цифра в несколько тысяч пар колонок видится более чем реальной.
На первом этапе «раскладушка» будущего корпуса раскрывается и проклеивается битумным покрытием. Кстати, что интересно — внутренняя сторона МДФ не «голая», а тоже покрыта шпоном, просто самым обычным, а не ценных пород дерева. Так по словам разработчиков достигаются несколько иные и нужные им свойства.
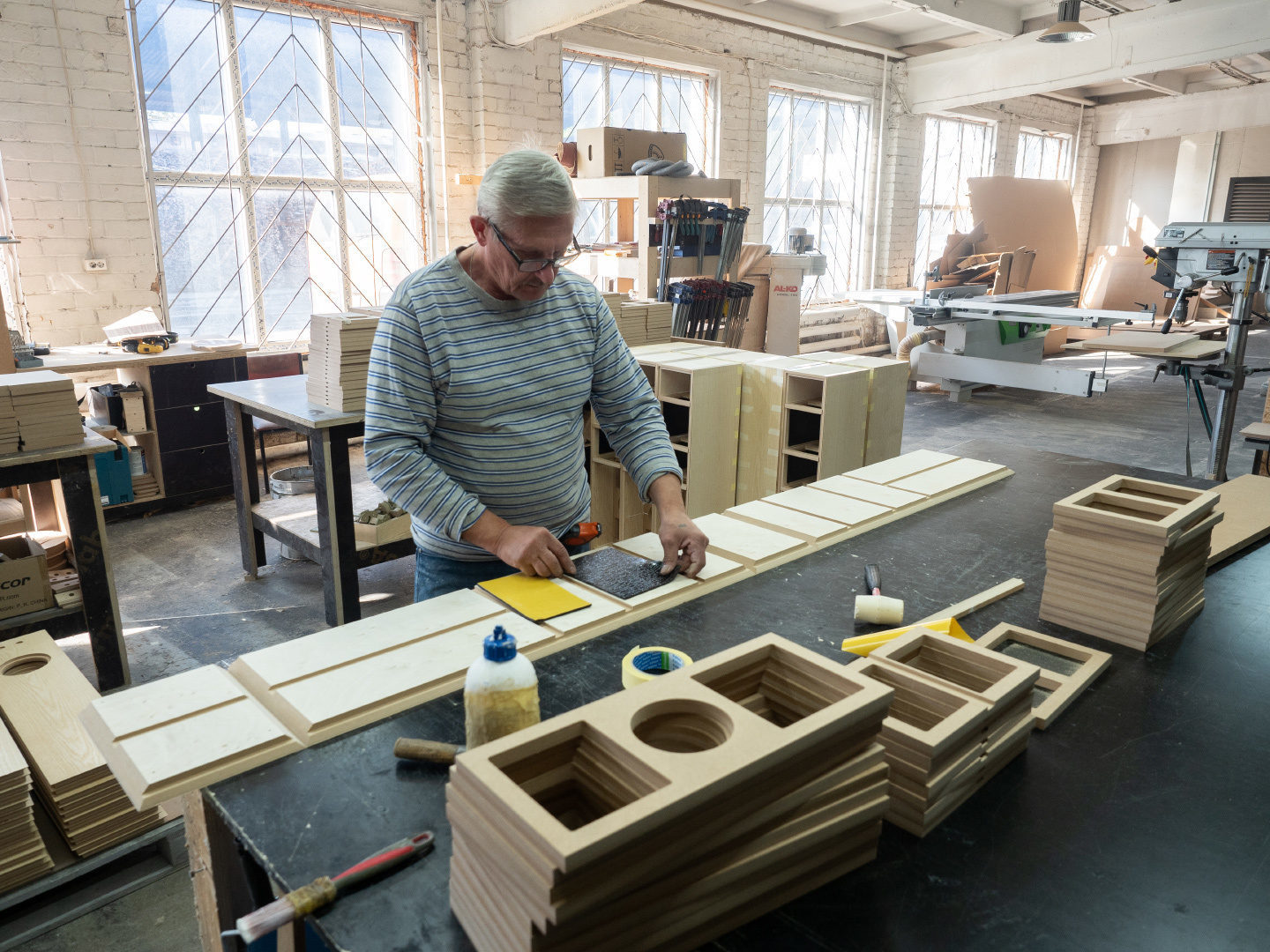
Дальше все собирается уже на клею и со всеми положенными распорками, после чего мастер переходит к следующему корпусу, а собранному корпусу нужно время, чтобы просохнуть перед дальнейшей сборкой и отделкой.
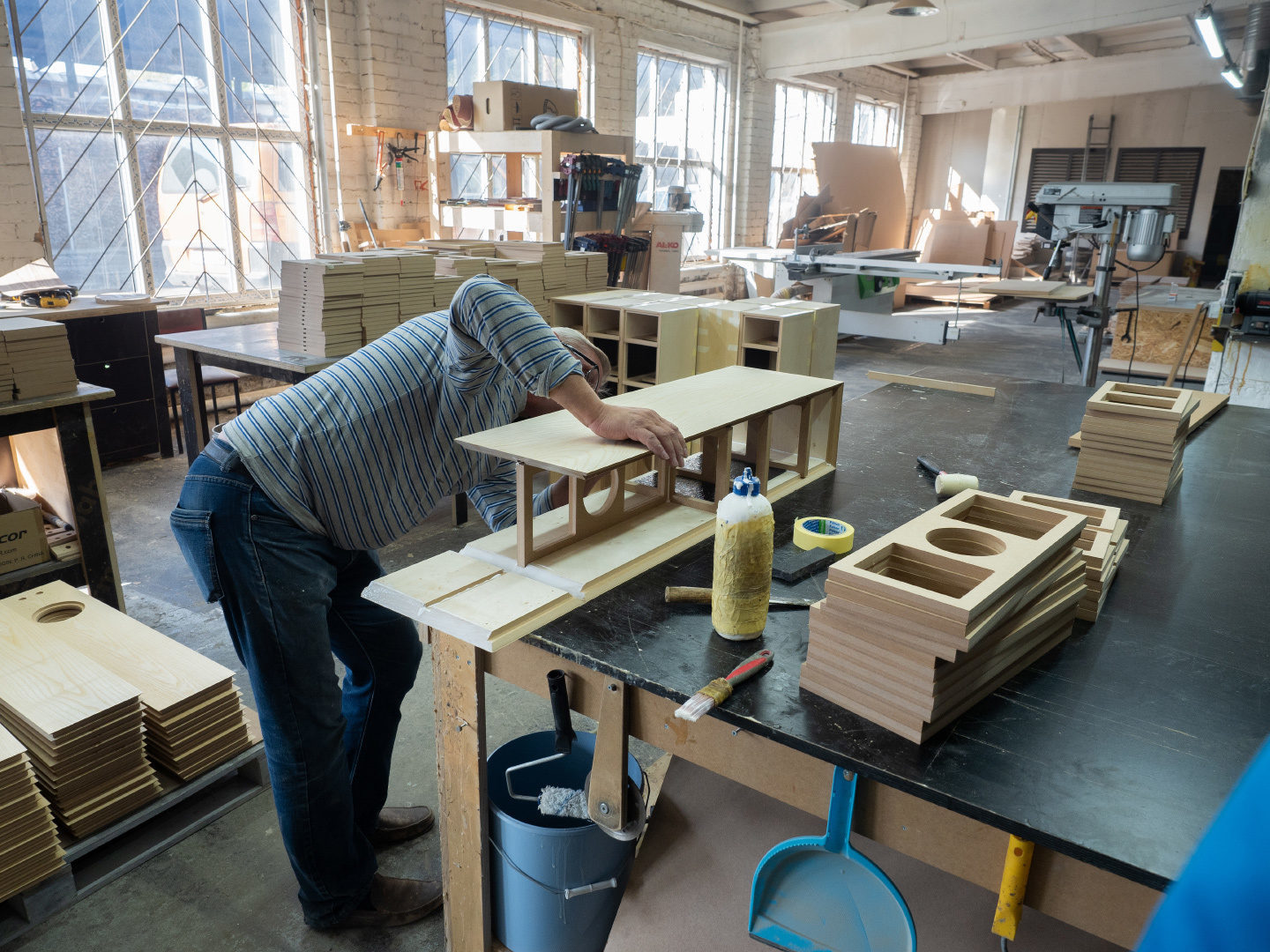
Можно заметить, что корпуса собираются не по принципу сразу всей коробки целиком — передние панели или, например, основания закрепят позже, на следующих этапах. Так что процесс получается не быстрым даже без учета сушки.
Производство же построено таким образом, что весь цикл работает то на одну модель, то на другую — в зависимости от заказов. Так, все цепочки логично выстраиваются одна за другой, но с привязкой к выпускаемой модели. Кстати, на этой фотографии тоже неплохо видно внутренний шпон.
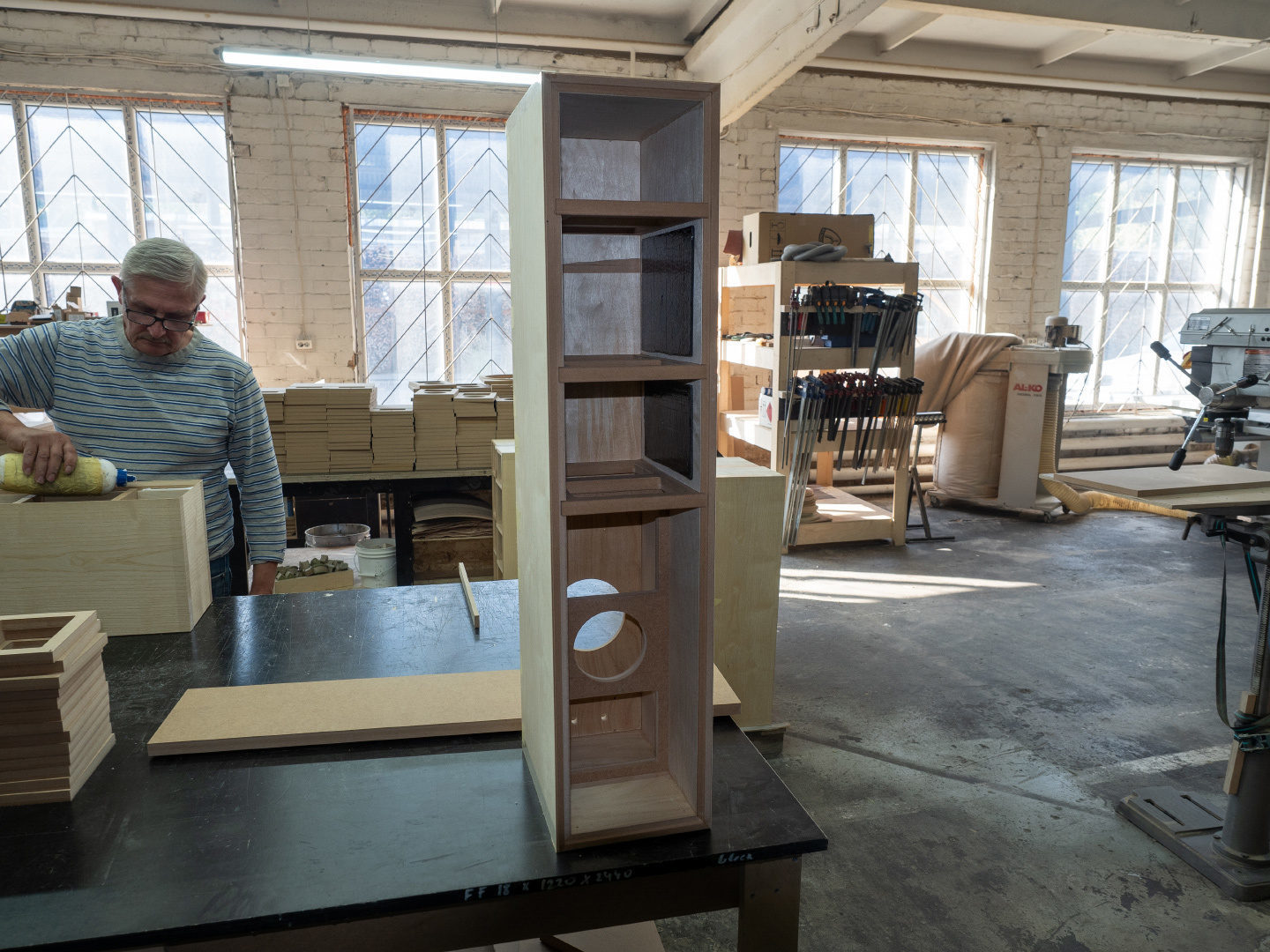
Передние панели крепятся позже не только потому, что стыкам логичнее просыхать не всем сразу. Вот тут можно увидеть, как отдельные панели, уже покрытые лаком, проходят шлифовку.
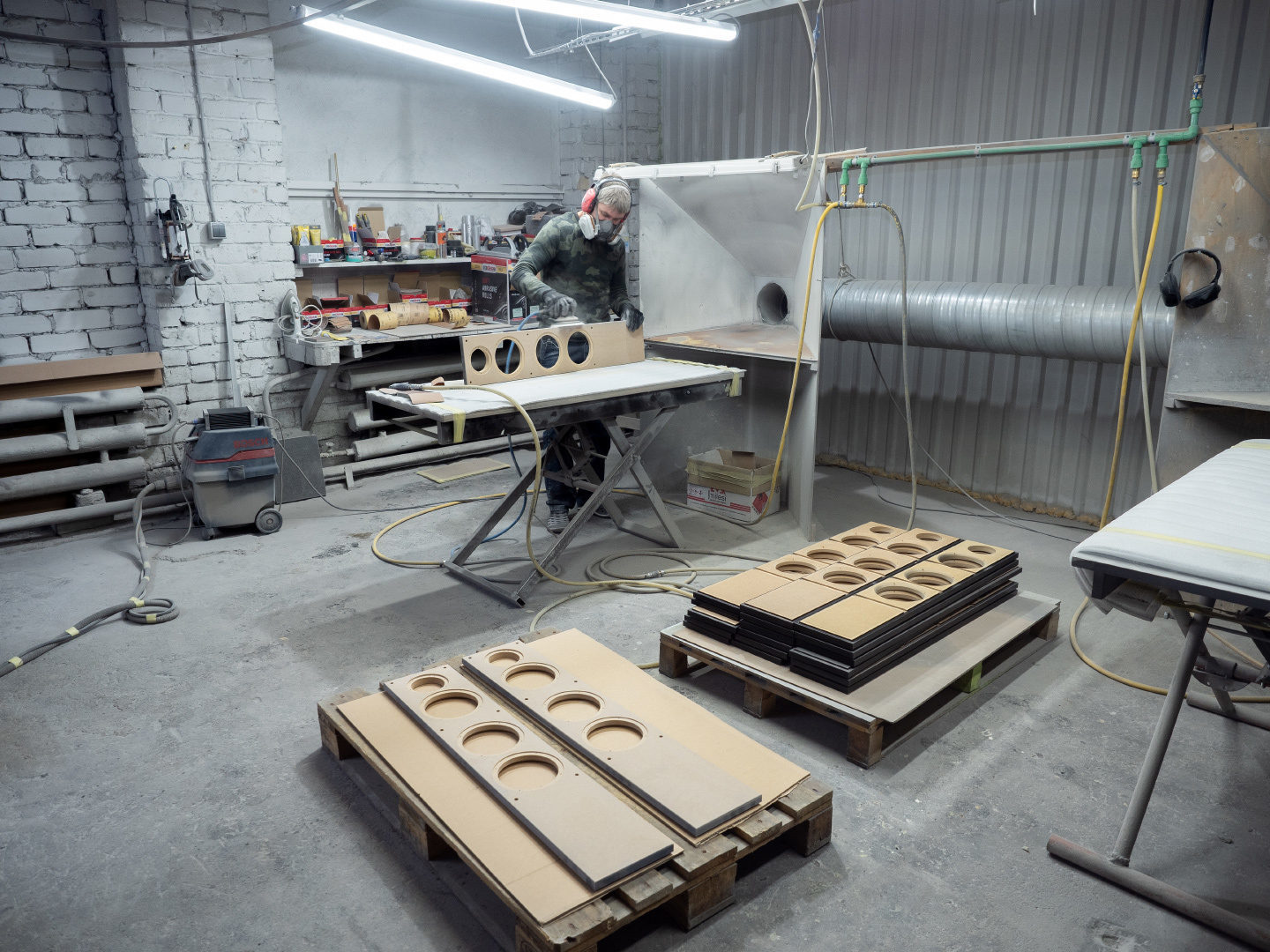
С корпусами, если кто не знаком с тонкостями производства, тоже не все просто. Например, на этапах отделки будущий черный лак выглядит не совсем черным и не совсем как лак.
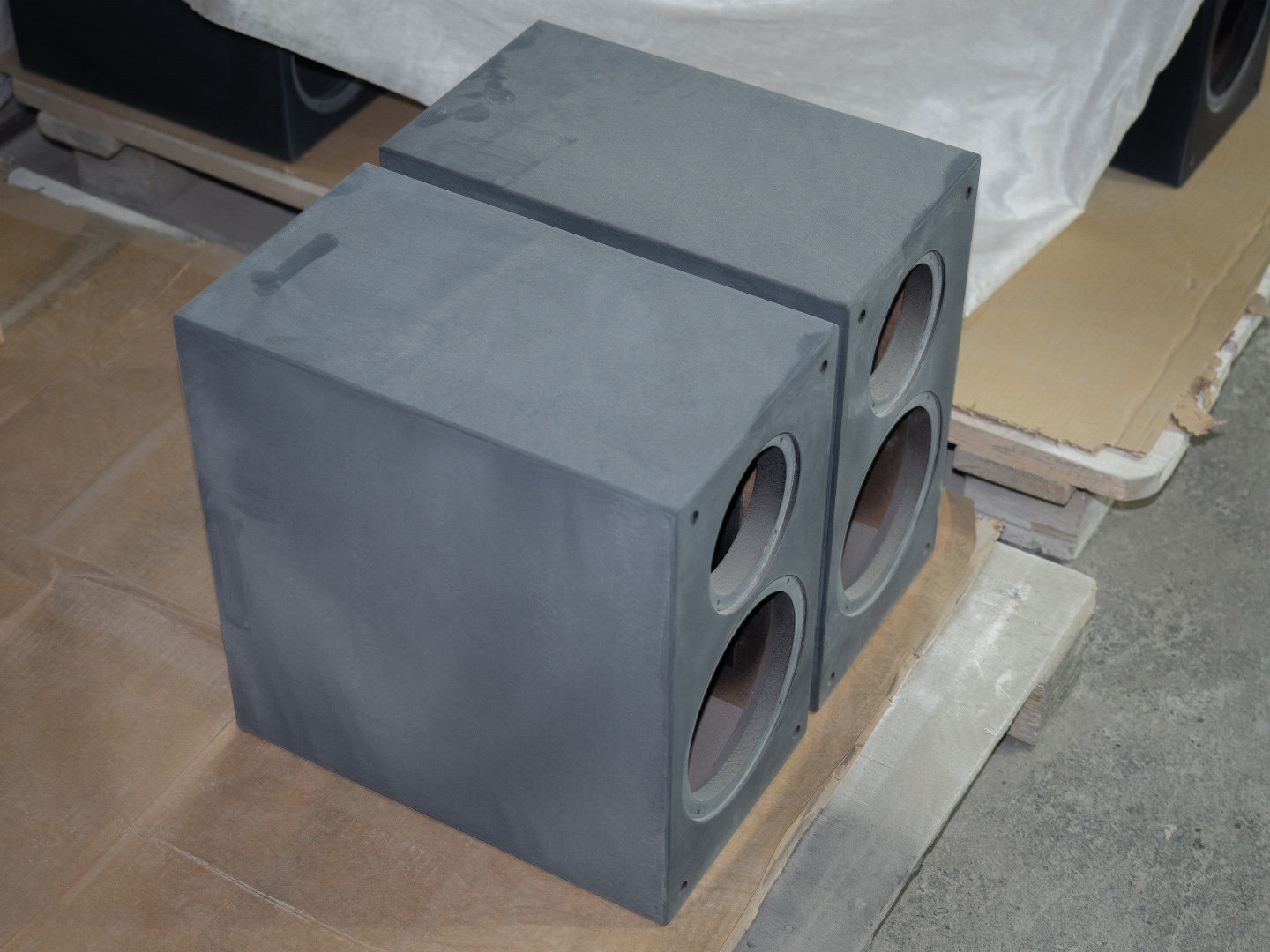
Хорошо многим знакомая отделка под названием «черный ясень» тоже в процессе обработки имеет несколько неожиданный вид. Потому что одним слоем дело никогда не обходится, а при промежуточных шлифовках образуется такой эффект.
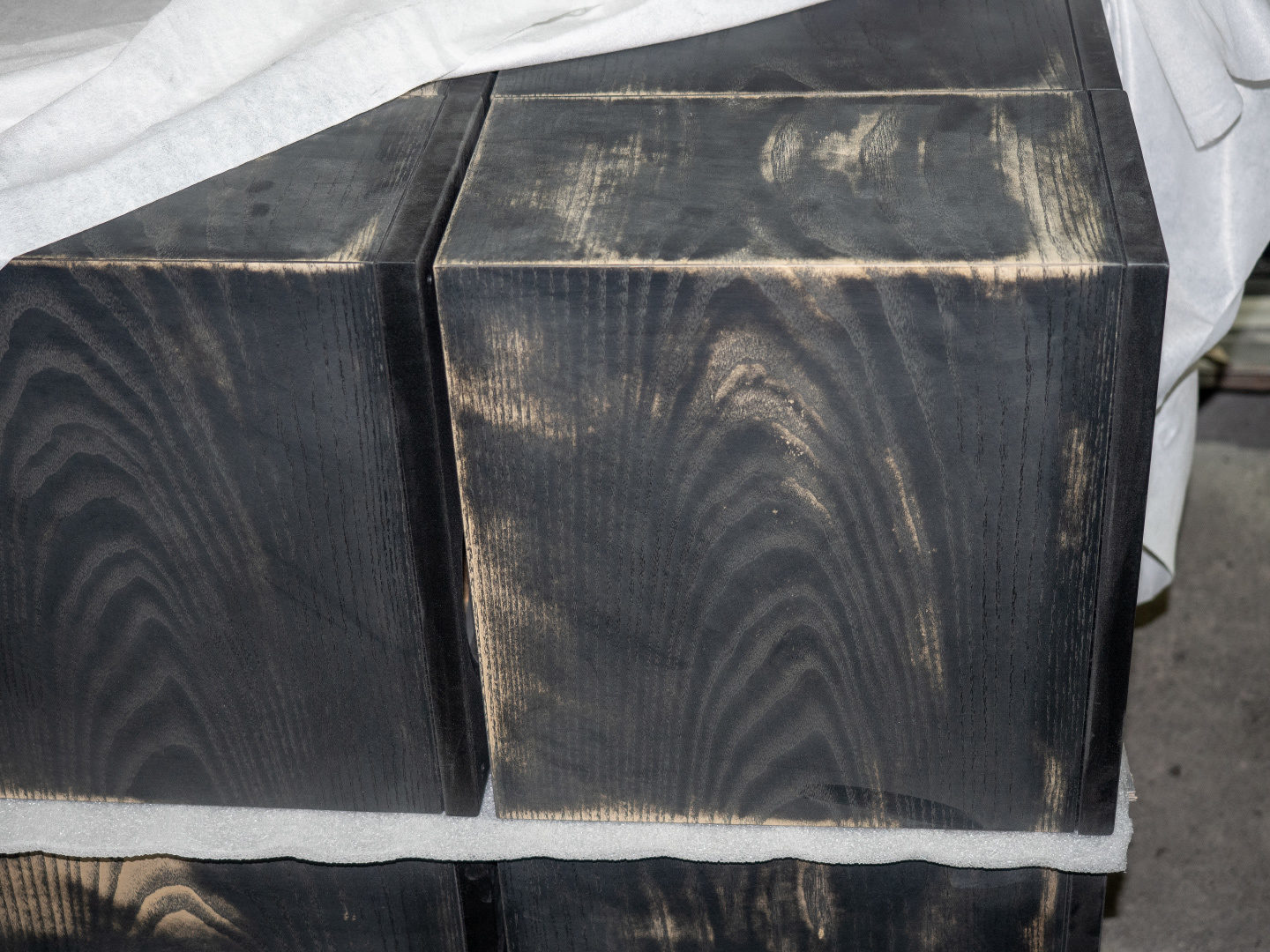
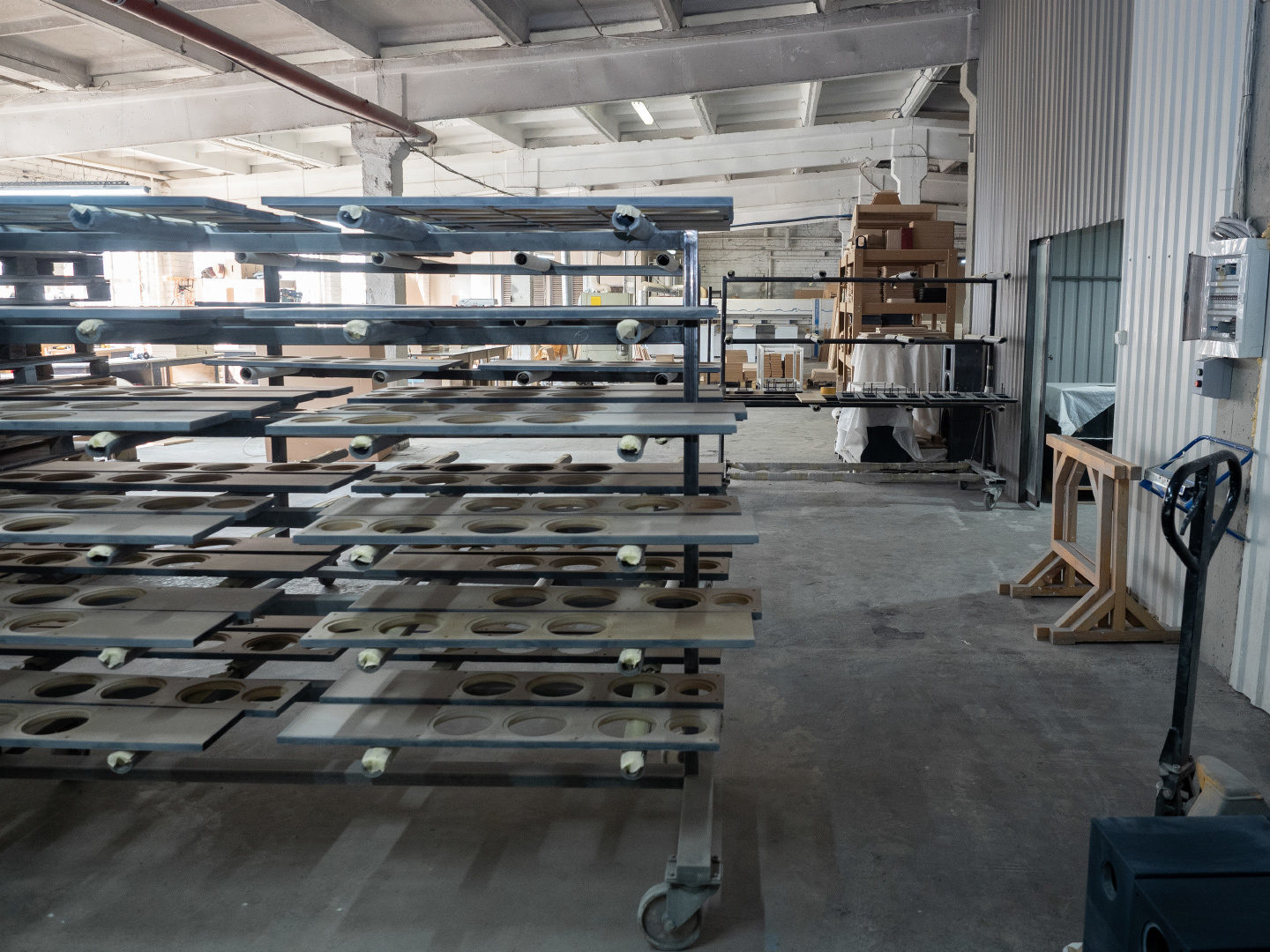
Отдельная часть цеха отведена для хранения заготовок передних панелей — для них требуются специальные стеллажи. Отдельно хранят и полуготовые корпуса, которым нужно будет прибавить слоев покрытия.
Лакокрасочный цех здесь выделен в совершенно обособленную самостоятельную единицу, но без этого никак. Интересно другое — здесь могут работать и работают с кастомными цветами, и как в хорошей автомастерской предлагают подобрать нужный цвет. Это может быть и не совсем обычный цвет, предназначенный для серийной линейки, и что-то малотиражное — в том числе и подобранное для особых случаев. Так что покраска начинается с подготовки самой краски.
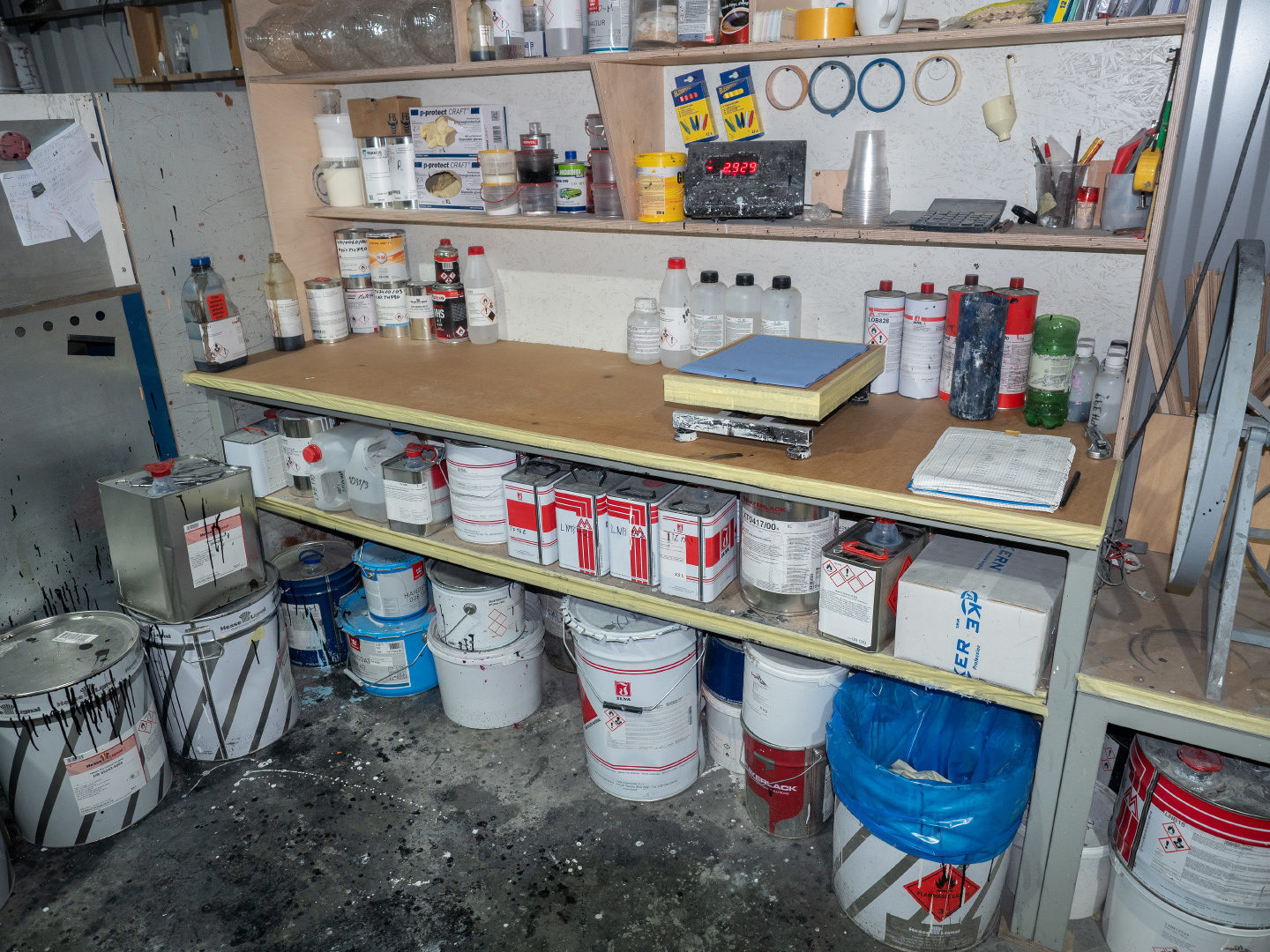
Этот аппарат все смешивает. Такие устройства иногда встречаются в магазинах, где можно самому купить краску и колер к ней. Но на производстве нужно все свое, да и масштабы побольше.
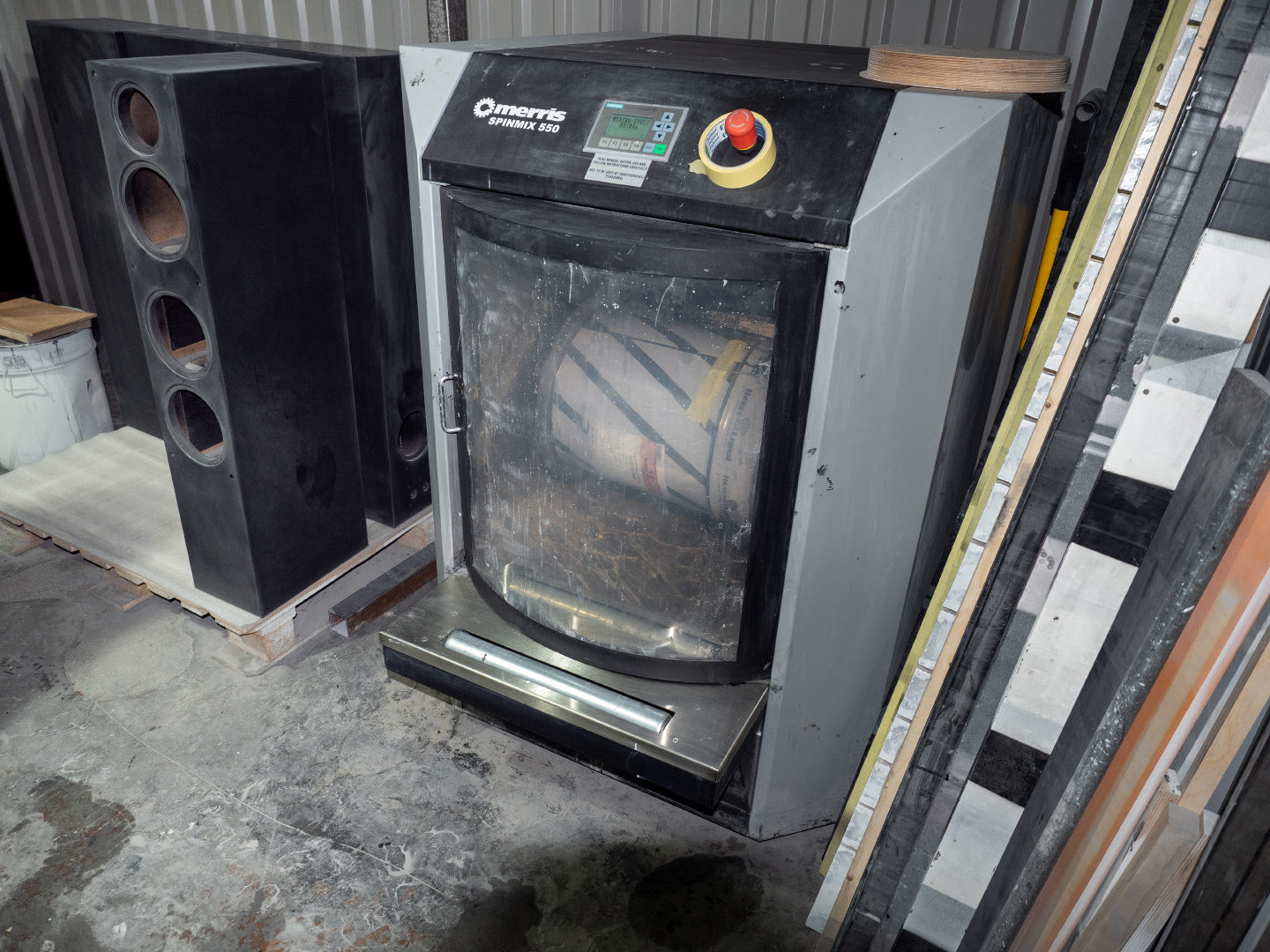
Процесс покраски или нанесения лака проходит в нескольких разных покрасочных камерах. Тут, понятное дело, все делается вручную. Вот так выглядит нанесение слоя лака.
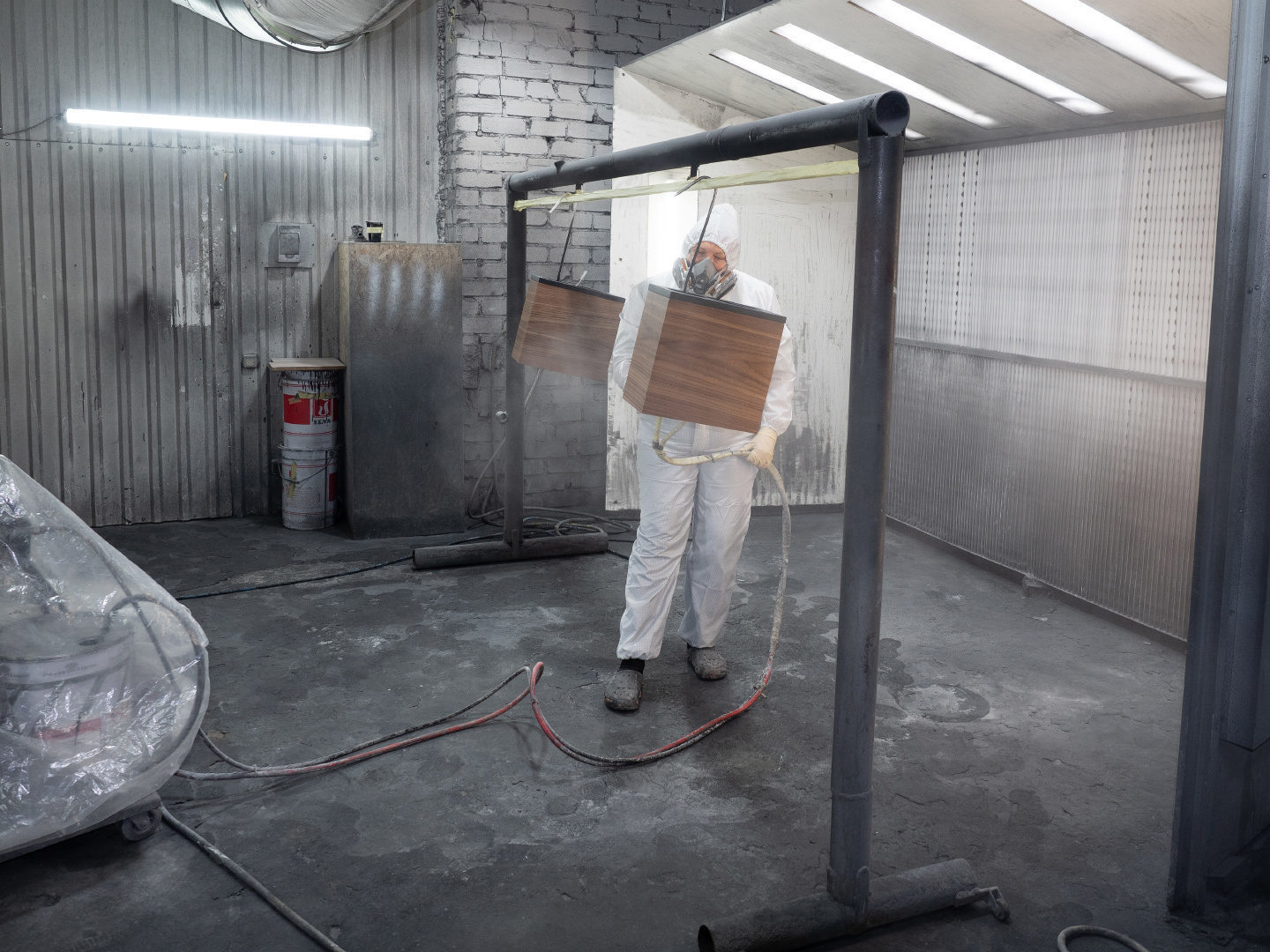

Через защитную дверцу сфотографирован процесс нанесения лака во второй камере. Она побольше по размерам и используется для крупной акустики.

Промежуточная сушка — для нее тоже отведена отдельная камера со своим температурным режимом. Сушатся одновременно и корпуса, и будущие полки аппаратной стойки Cold Ray.

А это ионизирующий антистатический пистолет из лакокрасочного цеха. Не все в курсе, но здесь проблема статики куда актуальнее, чем у винильщиков в быту. Чтобы ее устранять существует вот такое промышленное устройство, которое подает ионизированный воздух.
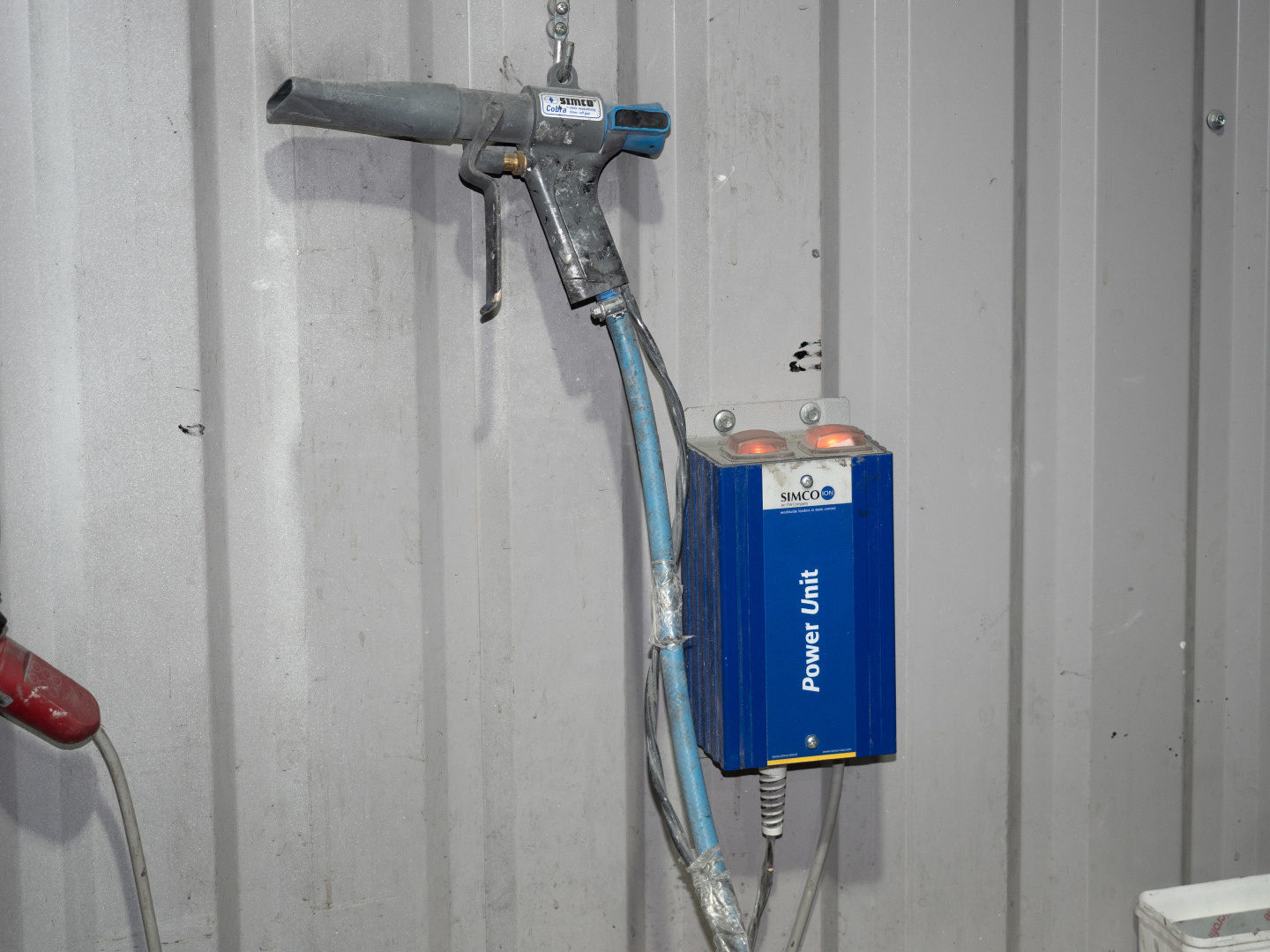
Полностью готовые корпуса в ожидании переправки из цеха в цех — здесь проходит разделение между той частью, где корпуса изготавливают, и той, где, собственно, собирают акустику до готового и упакованного изделия.
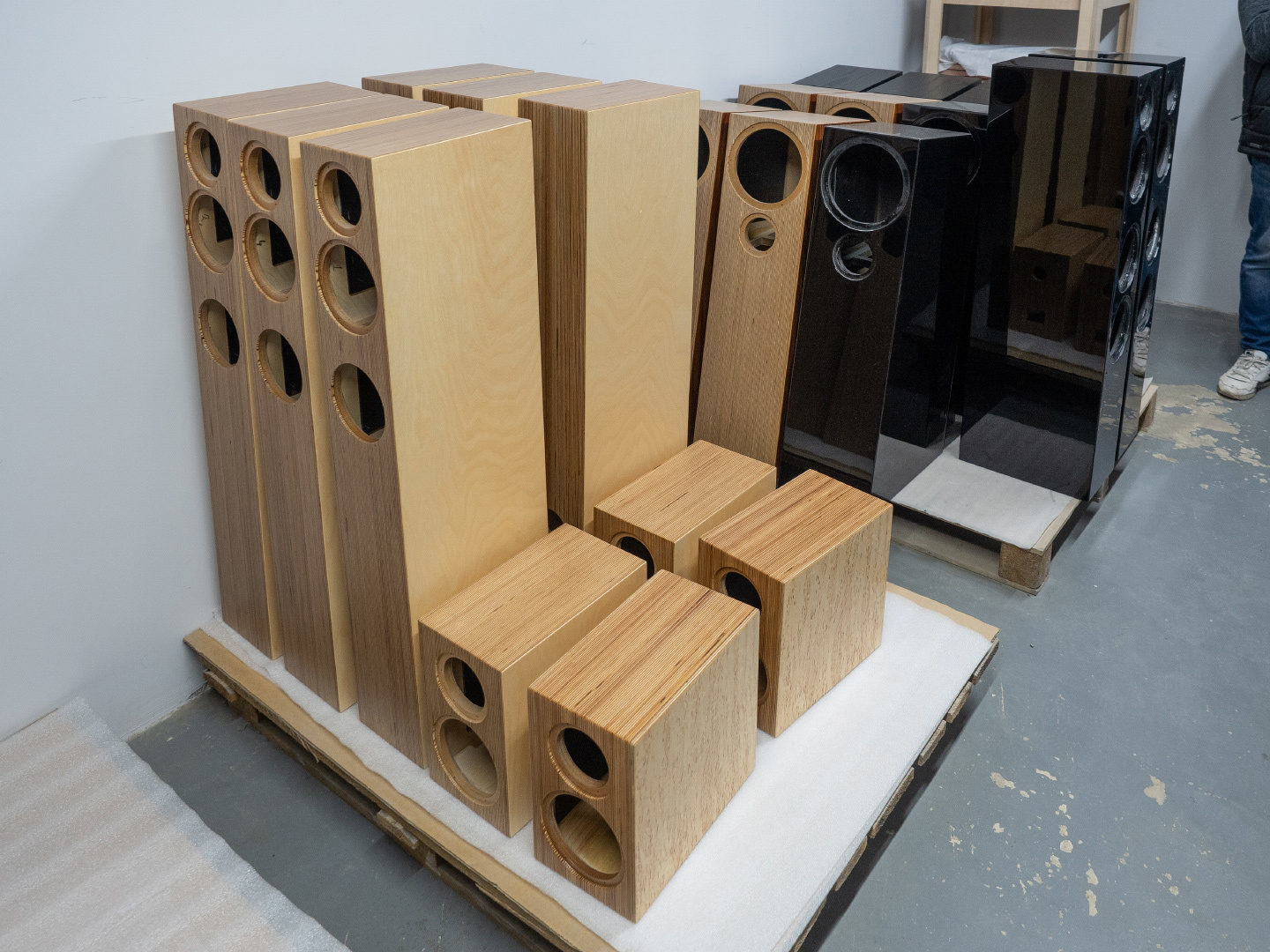
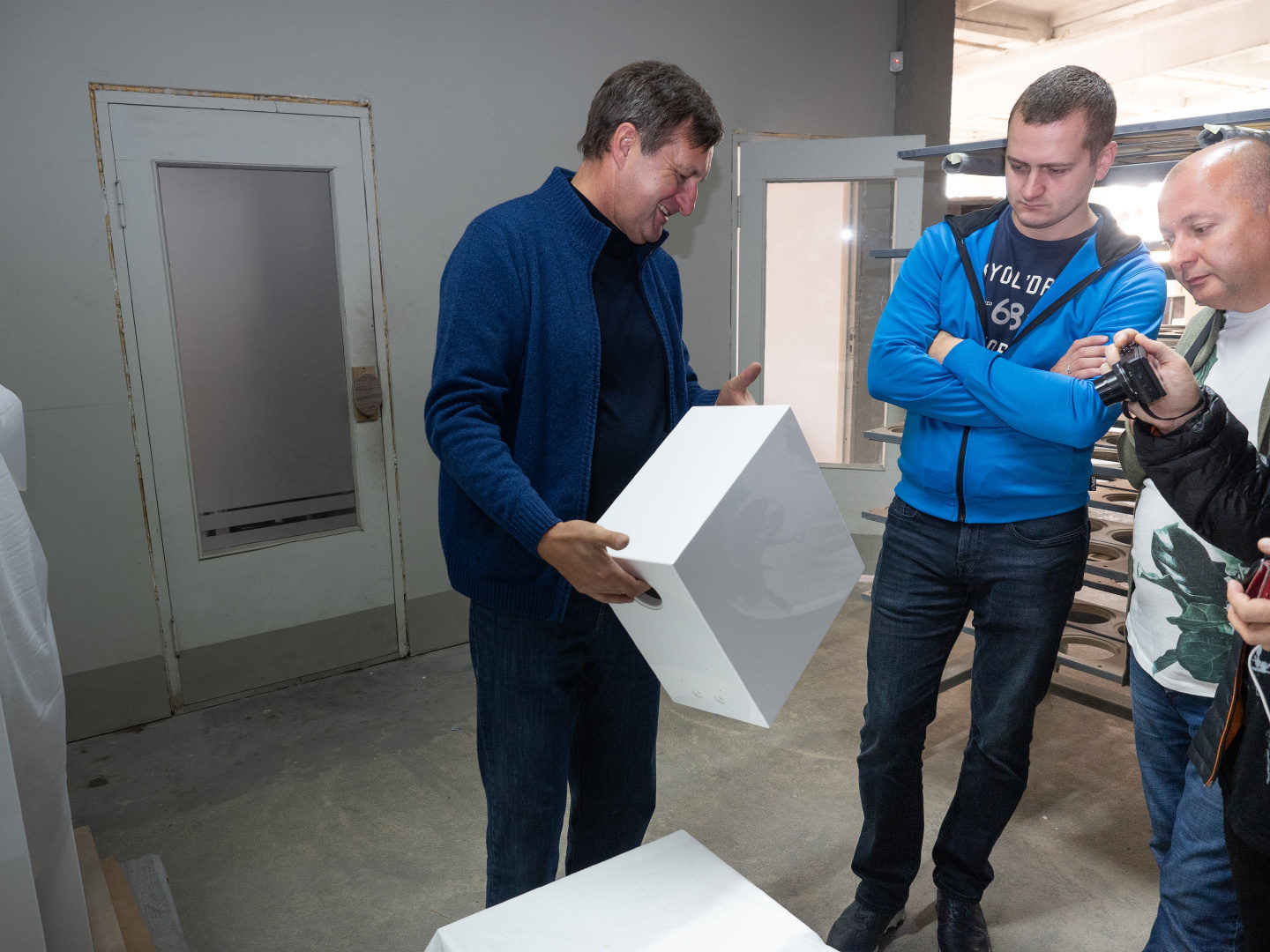
А вот те самые кастомы в необычной окраске. Оранжевые и бордово-вишневые — на выставках мы видели похожее. Но вообще, на такие цвета приходится совсем небольшой объем производства.
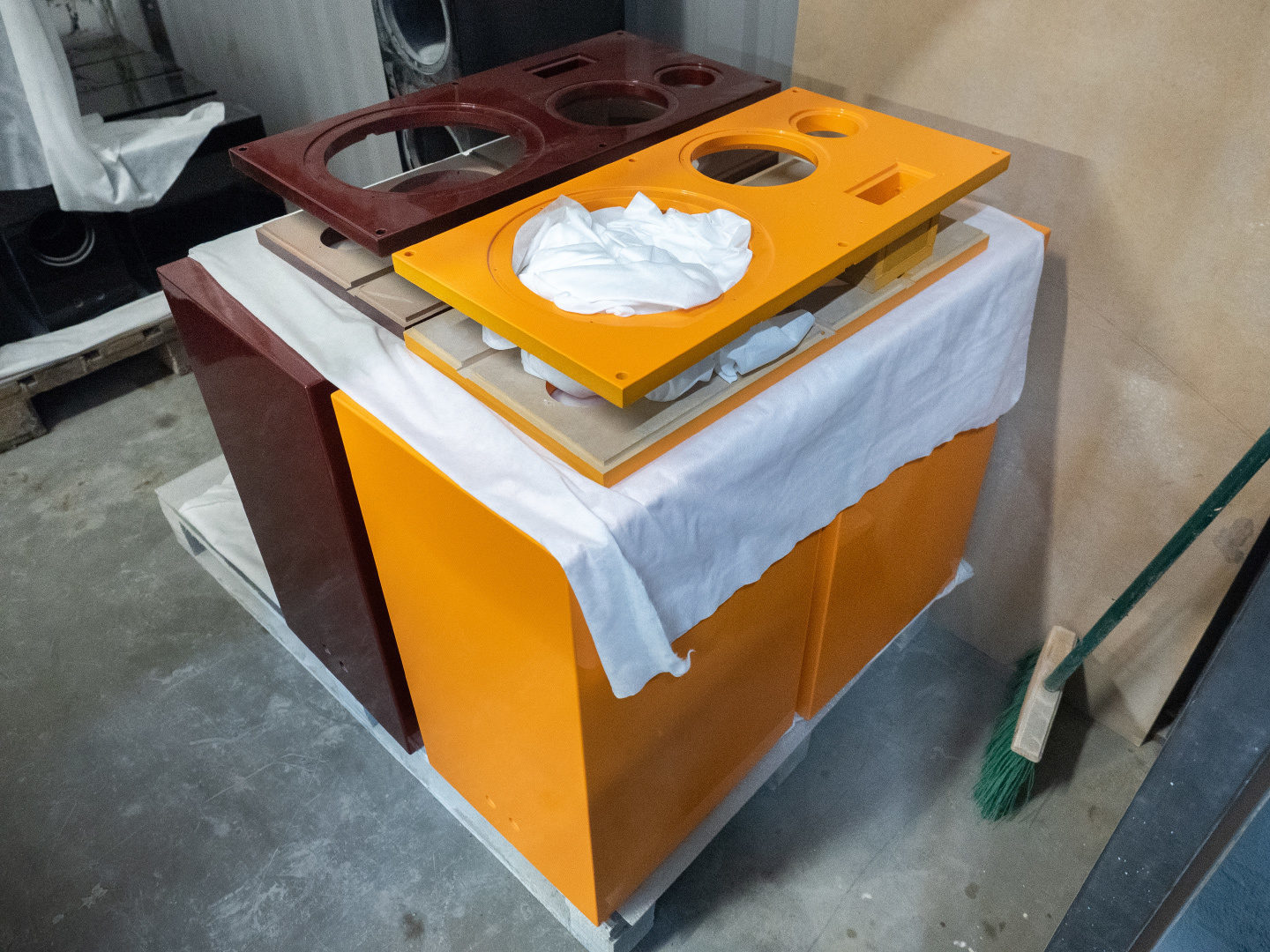
Первое, что бросается в глаза в сборочном цеху — запасы комплектующих. Многие динамики заказные, а чтобы оформить заказ у производителя, нужно заказывать партии от нескольких сотен до нескольких тысяч штук. Впрочем, все заказываемое на производстве расходуется — кроме того, что идет в запасы на случай дальнейших гарантийных и не гарантийных случаев, а также небольшого количества выбраковки. Она иногда случается, но немного — все-таки комплектующие не младшего уровня. Но проверить-то никогда не помешает.
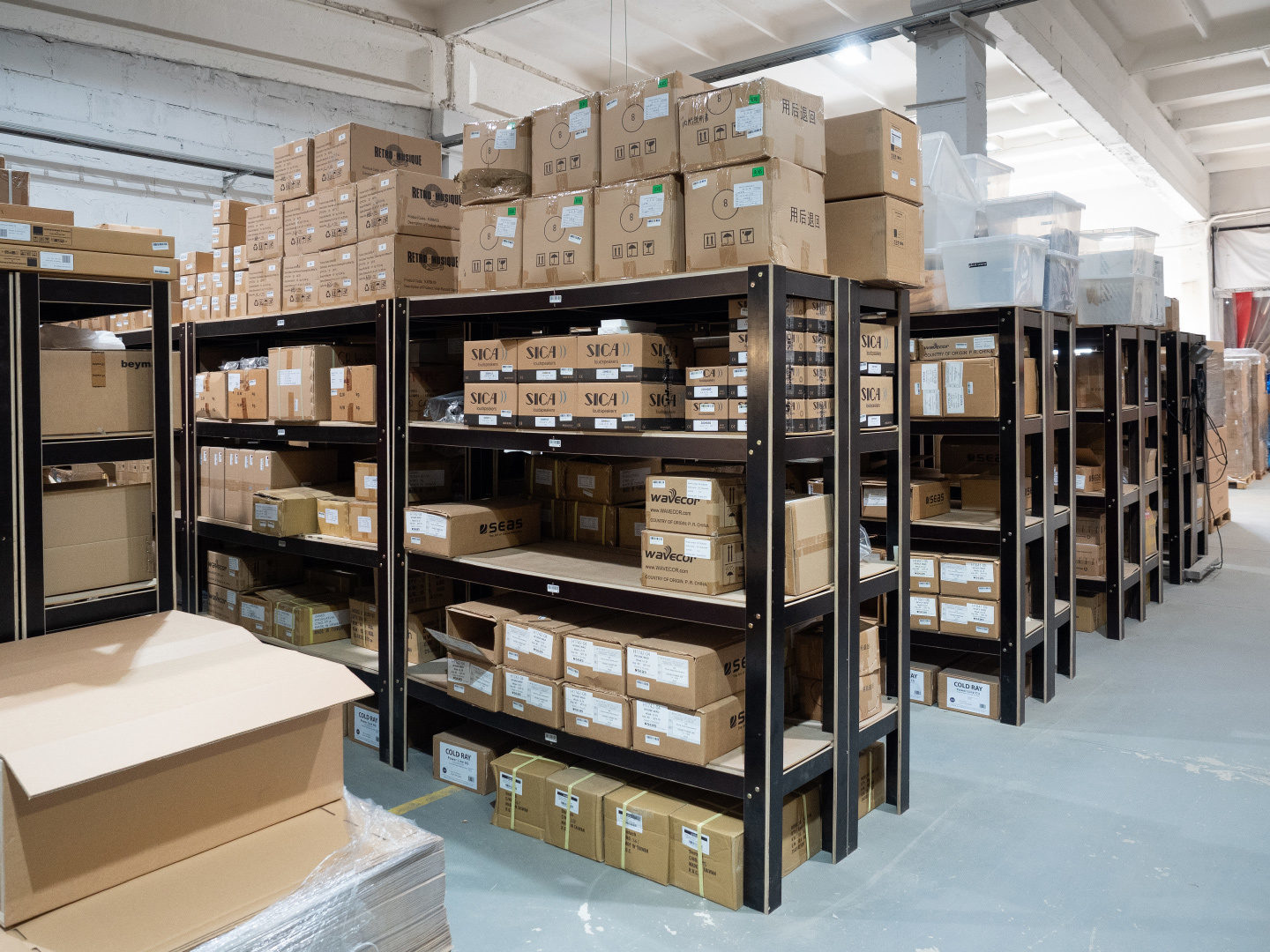
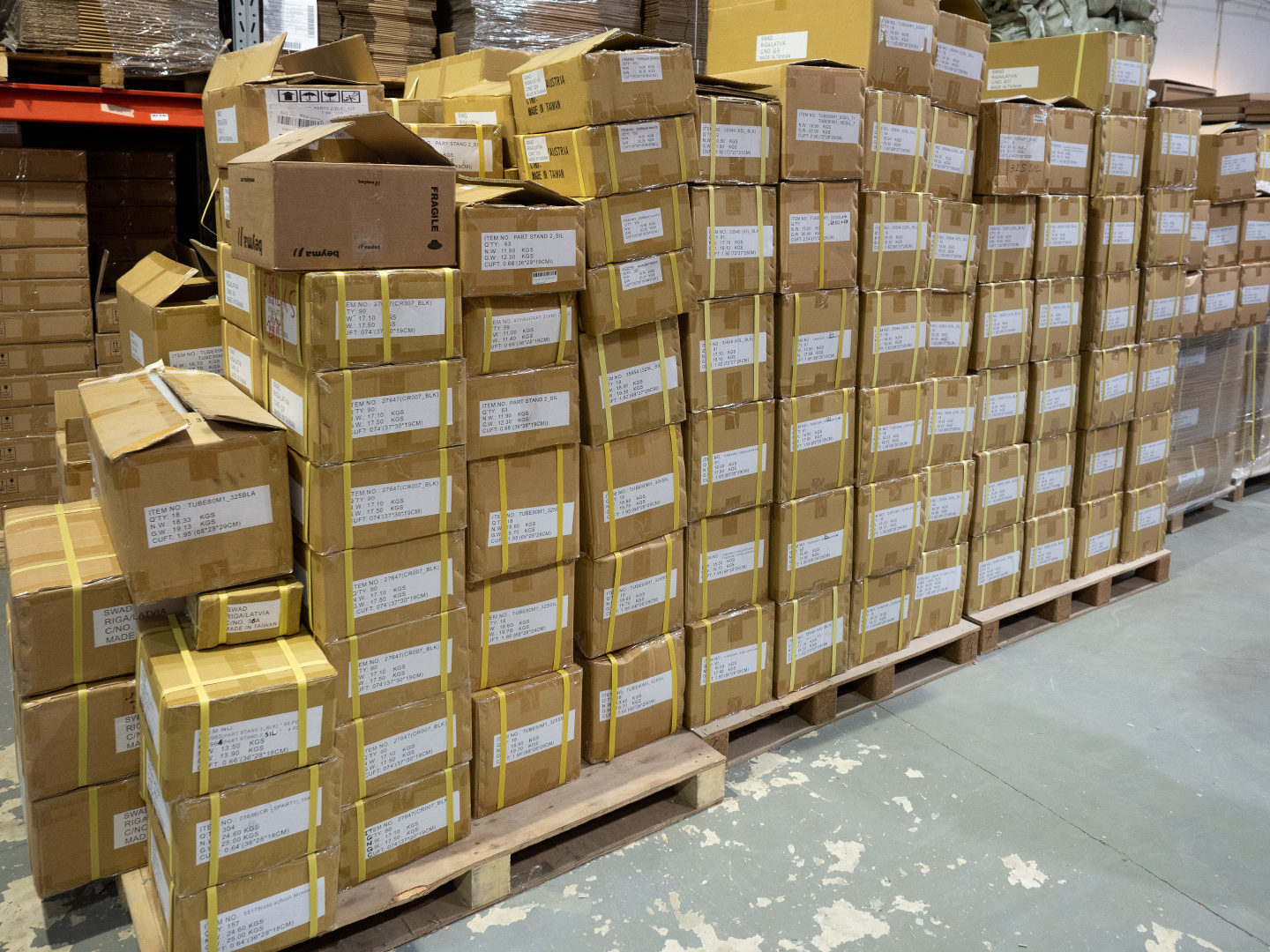
Прежде чем собрать акустику, нужно собрать остальные ее комплектующие. Например, защитные грили. Их рамки выпиливаются и красятся на заводе (и это не пластик), ткань и крепеж приходит от поставщика. Сборка осуществляется на месте.
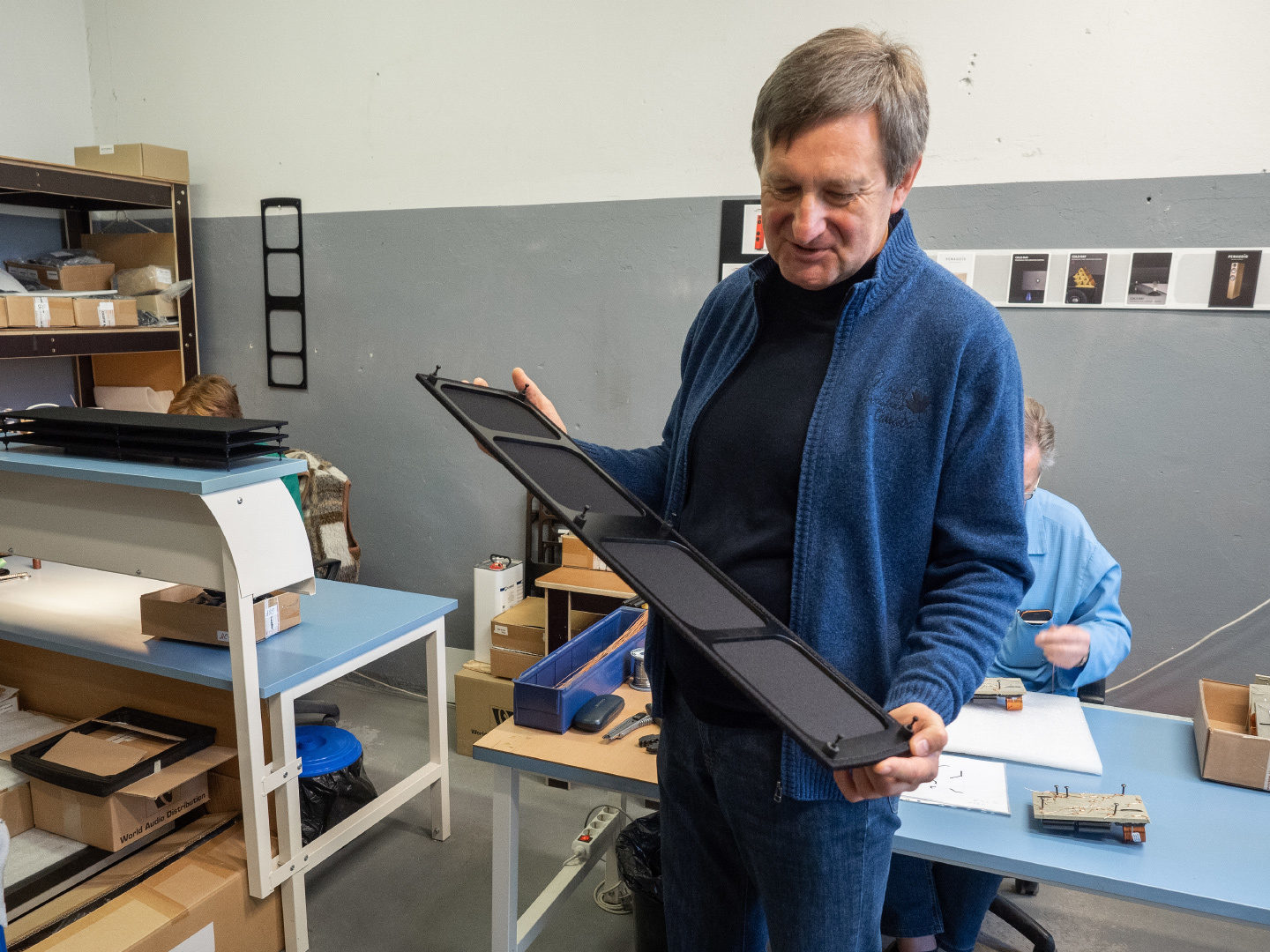
А вот здесь собирают фильтры. Вручную, по шаблонам, навесным монтажом. Выглядит все это весьма убедительно. И сам процесс.

И результат.
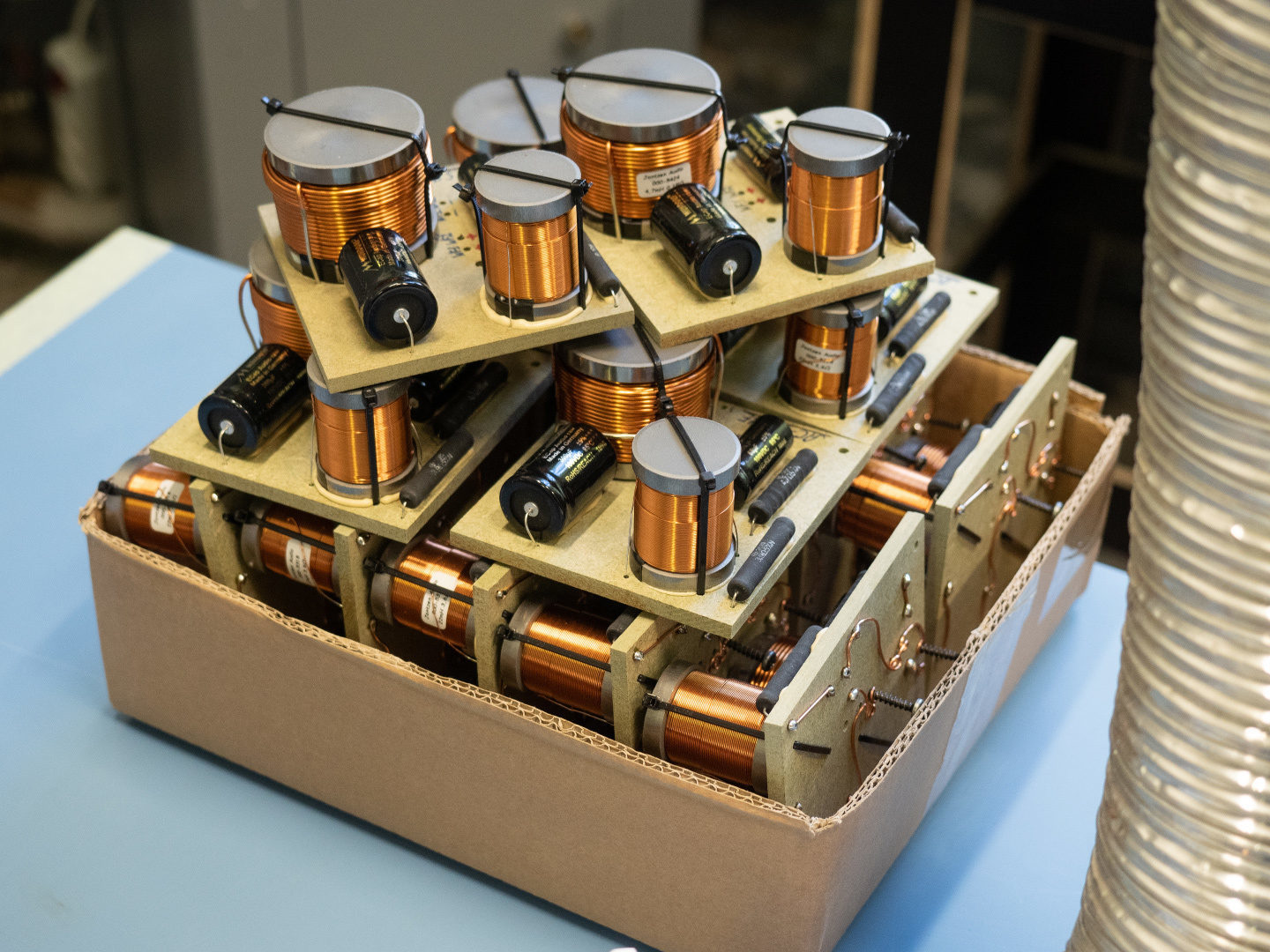
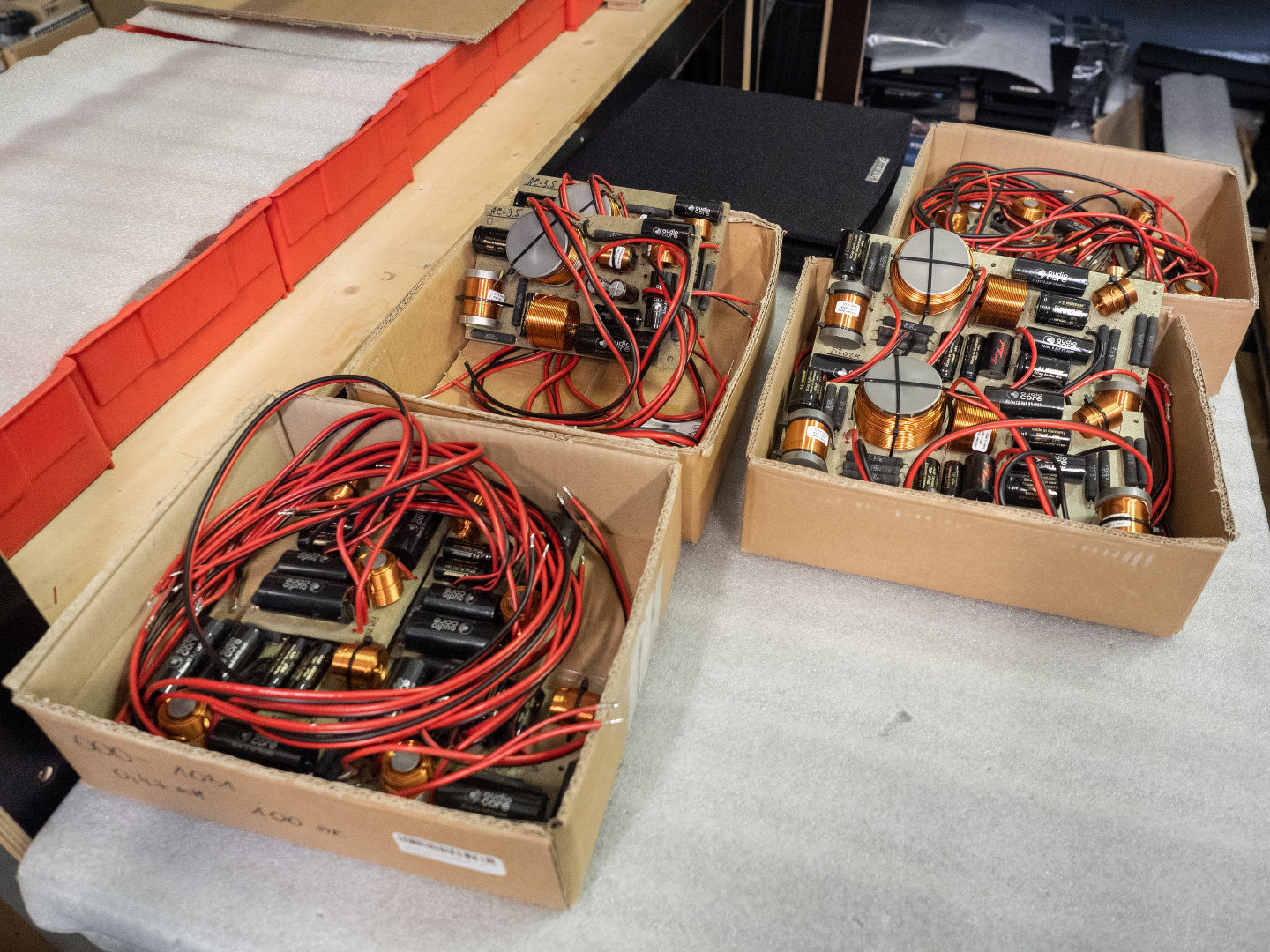
Ну а если говорить о кроссоверах моделей постарше, то вот примерно так они выглядят. Это комплект на пару колонок.
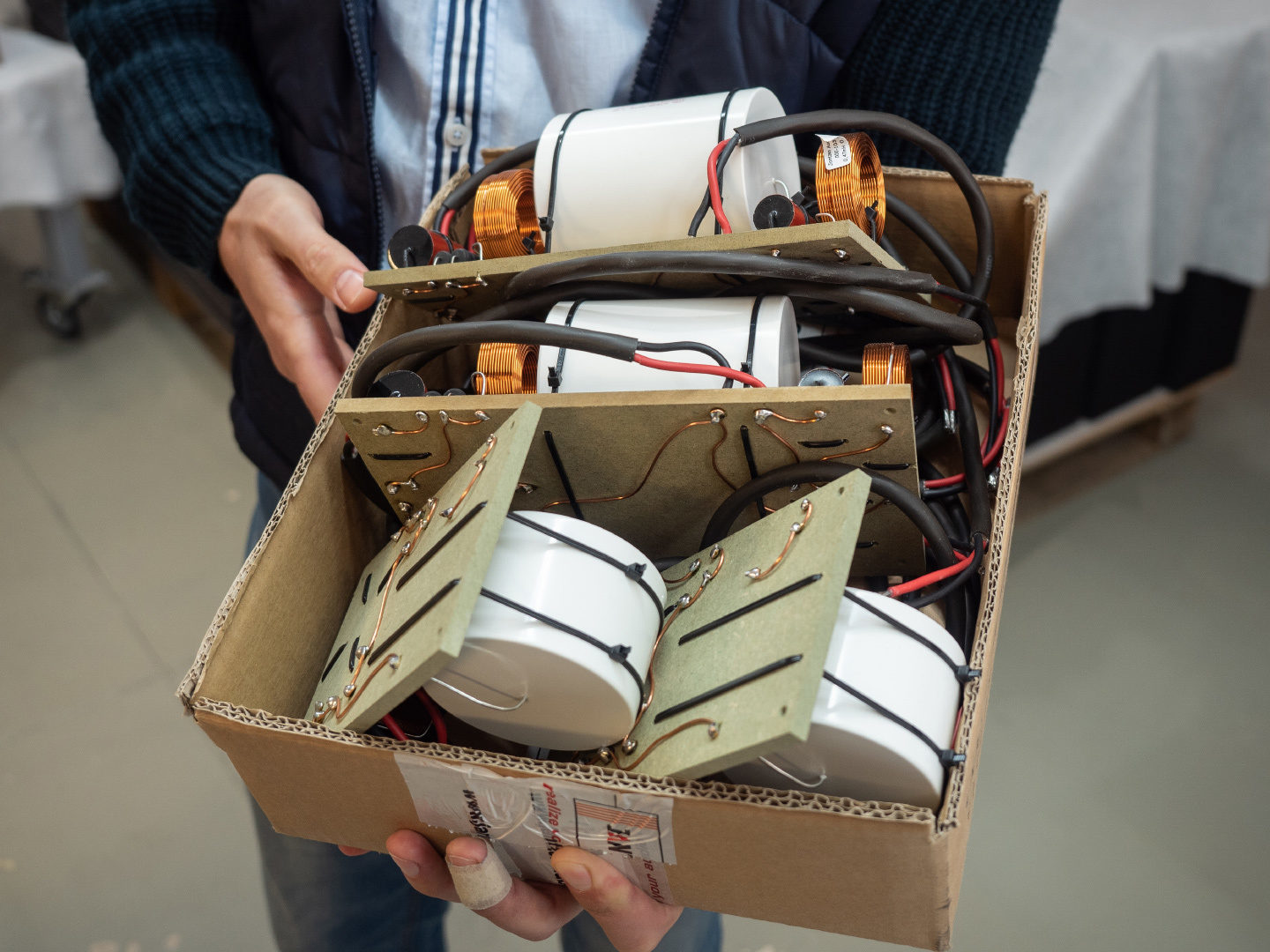
Сборка на том этапе, когда в акустику устанавливают динамики, происходит не на конвейере. Точнее, тут получается нечто типа полу-конвейера: вместо ленты используются вот такие столики на колесах, на которых акустика переезжает от одного сборщика к другому. В результате, все получается достаточно удобно для небольшого производства и вполне эффективно при имеющихся объемах. Я рассмотрел полусобранные экземпляры вблизи: качество более чем на уровне — все аккуратно не только снаружи, но и с изнанки.
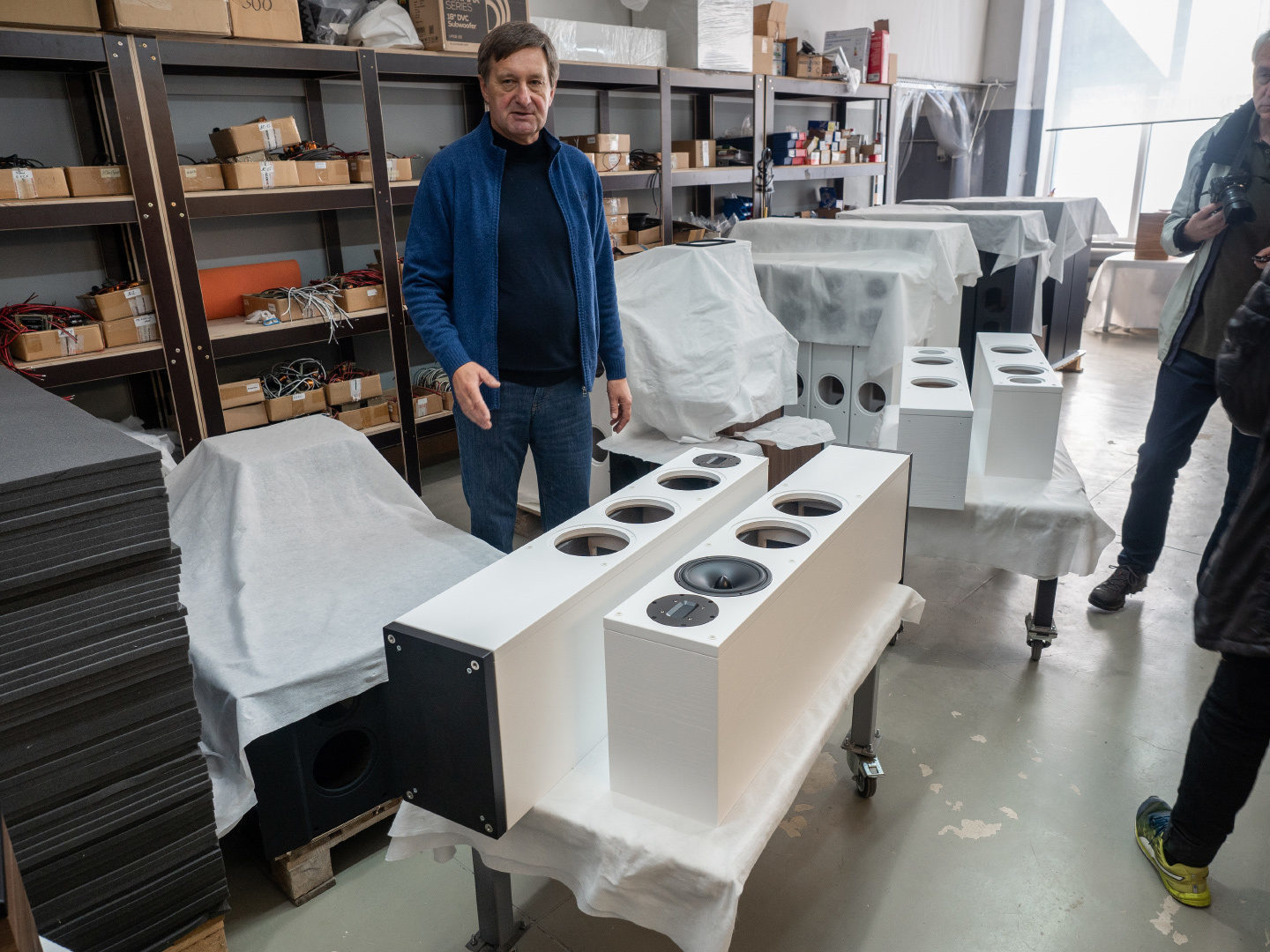
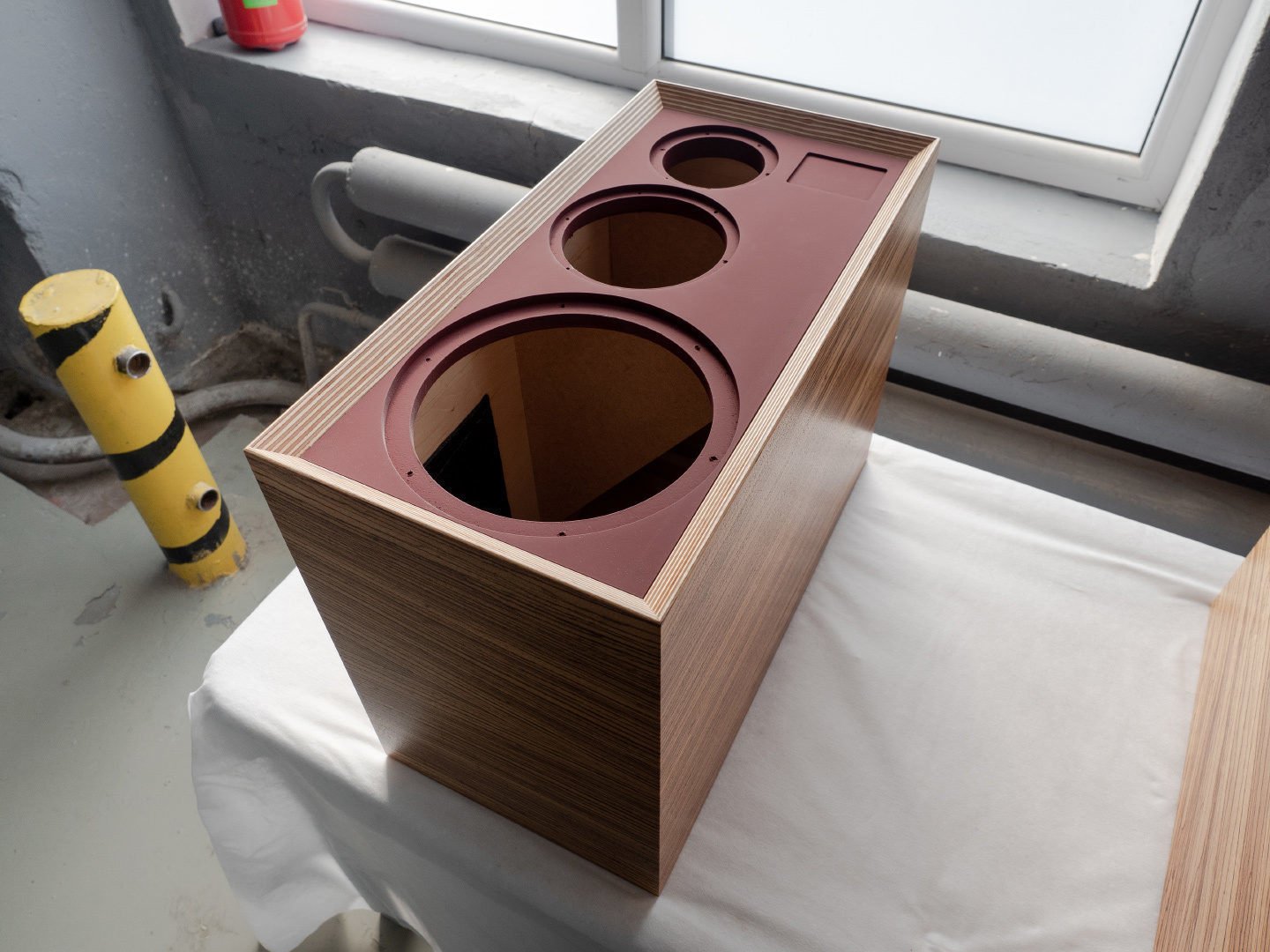
Еще немного сборочных процессов.
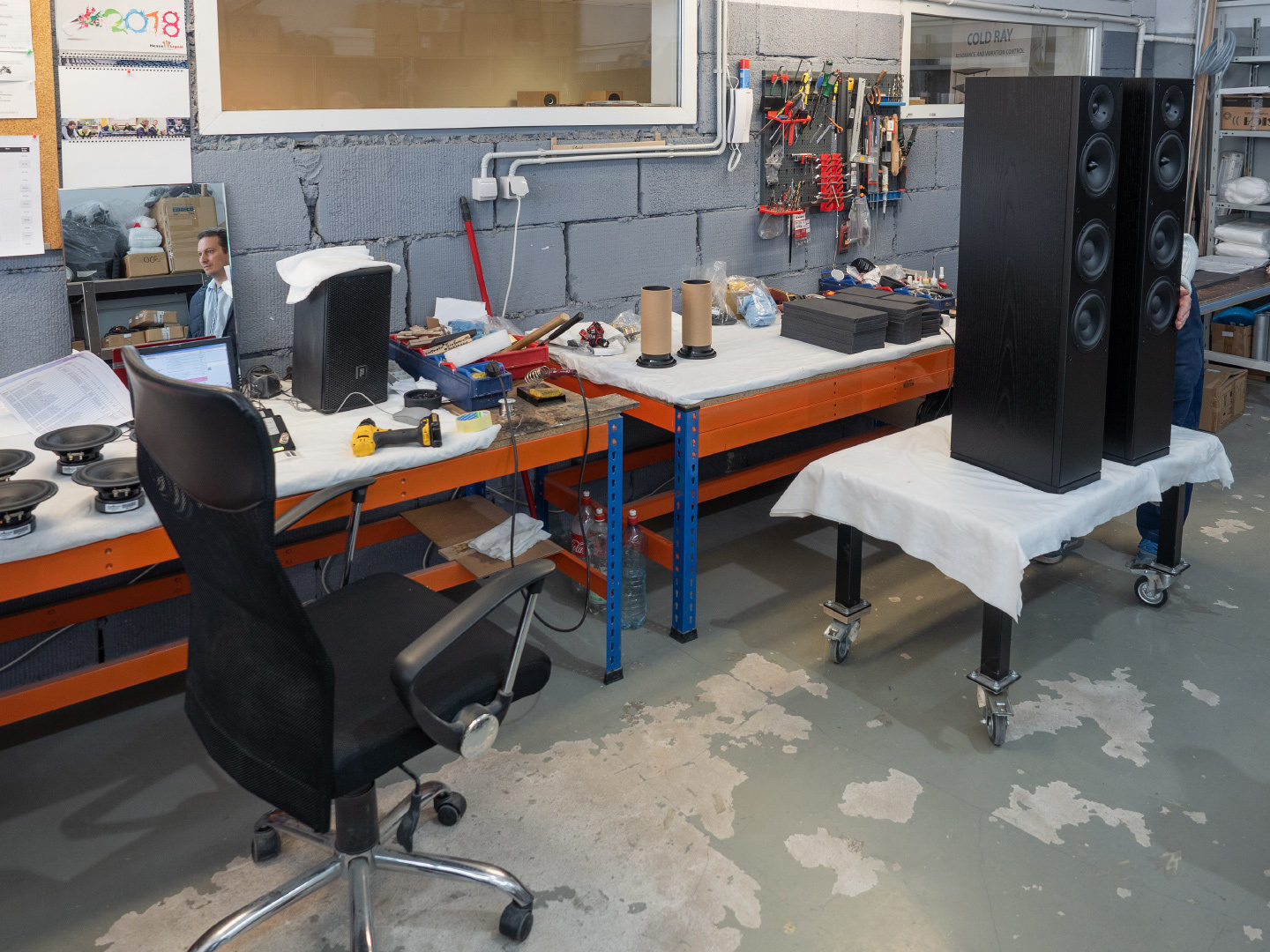
Одна из систем измерительного контроля. Отдельной камеры здесь нет. Впрочем, если контроль проходят все комплектующие в процессе, а для каждой модели готовой акустики есть профиль, в который должны укладываться измерения, то задача не видится невыполнимой. Тем более, что при небольших не конвейерных объемах замерам можно уделить больше времени.

И после всего — индивидуальная маркировка, присвоение серийных номеров и занесение их в базу данных. Как положено, на каждую выпущенную колонку есть своя учетная карточка с указанием комплектующих и с измерениями.
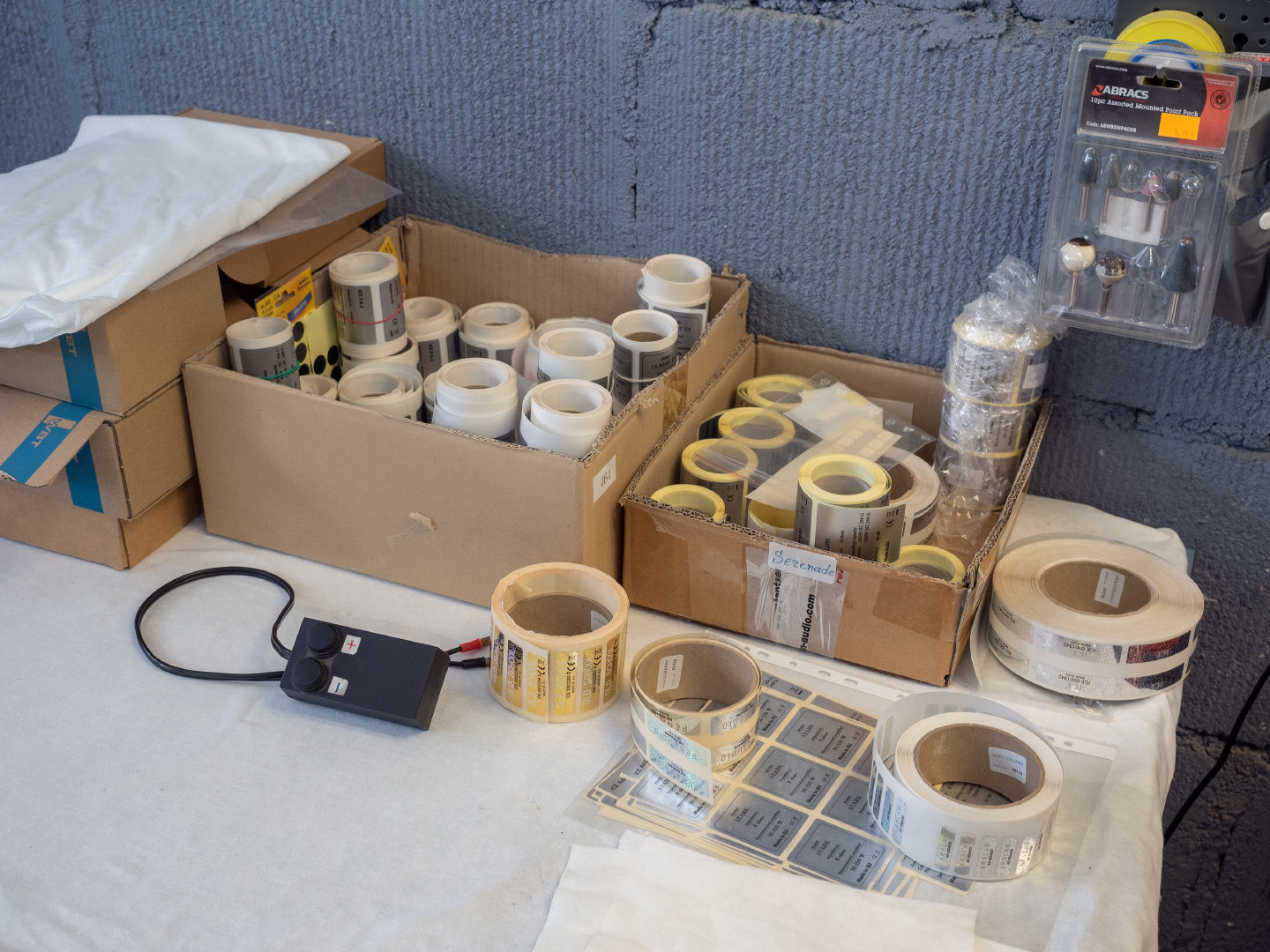
Ну что, пришло время все упаковывать? Этому тоже уделили внимание. Особенно с учетом того, что часть продукции уезжает к покупателям через пол-мира. Усиленные коробки, или скорее ящики, например, для собранных Penaudio.
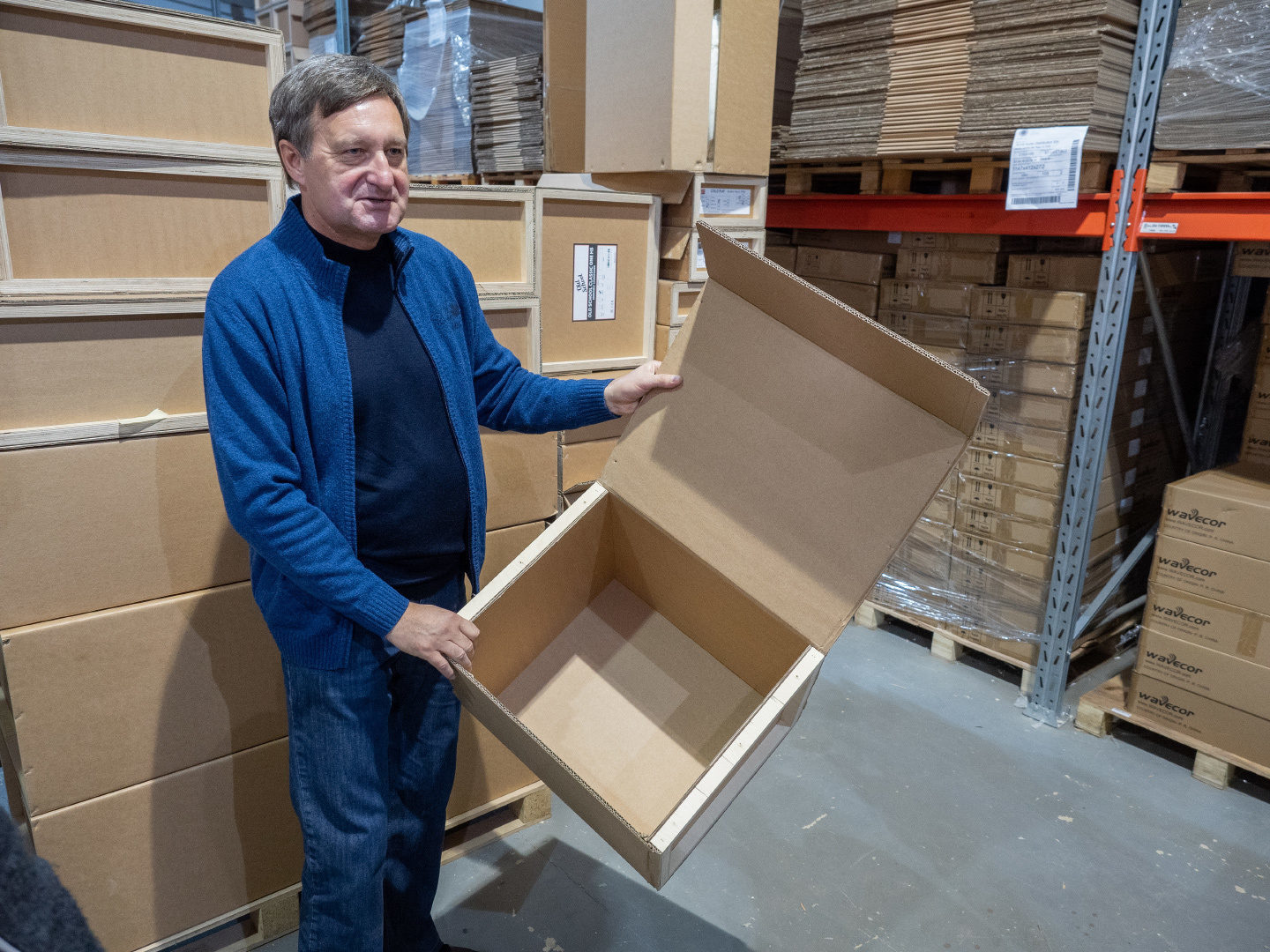
Или вот такое устройство, заливающее в пакеты полиуретан.
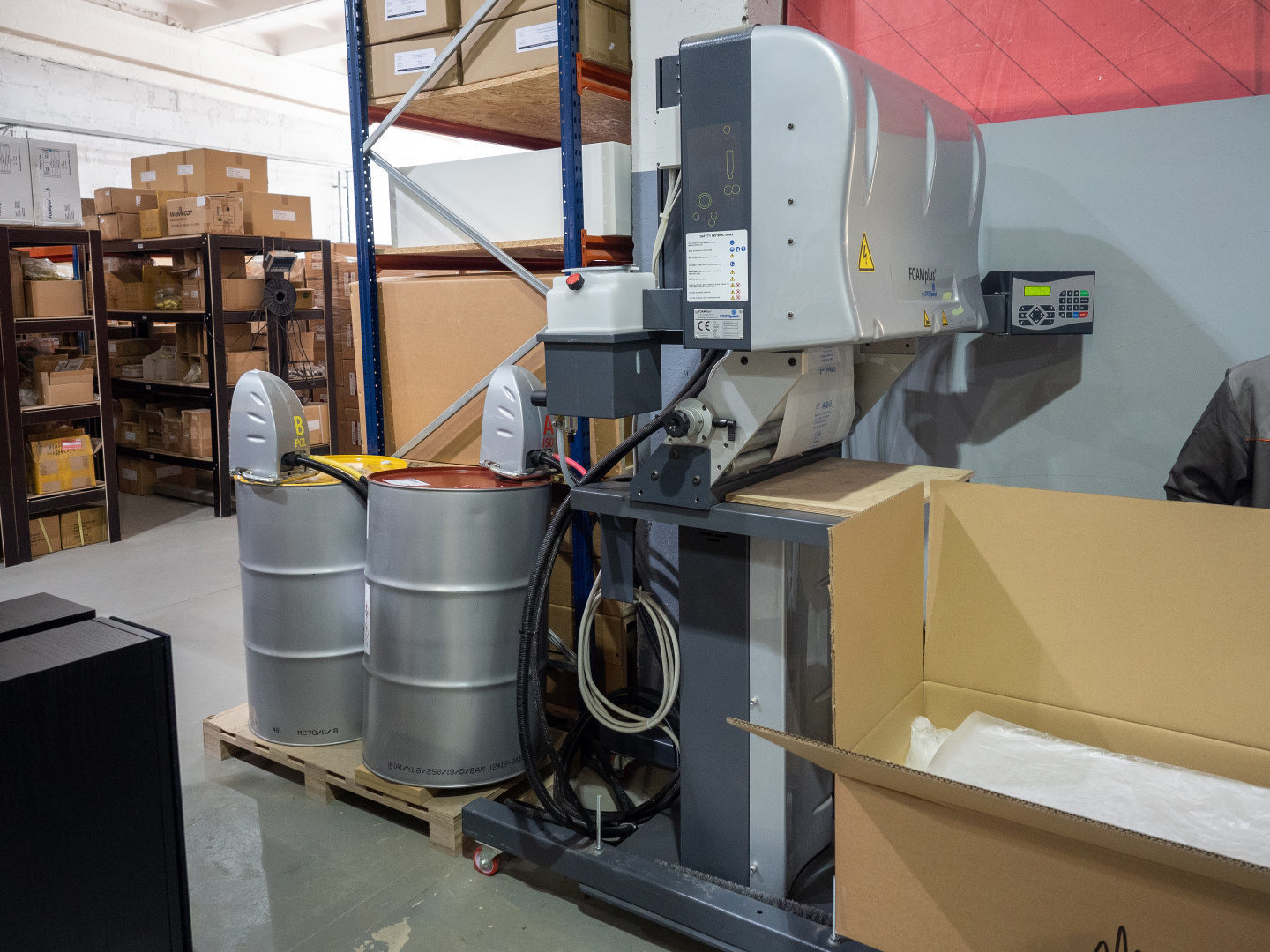
Пока коробка открыта, туда можно свободно уложить пакет, но пена в это время продолжает вспениваться в замкнутом объеме и формирует надежную защиту.
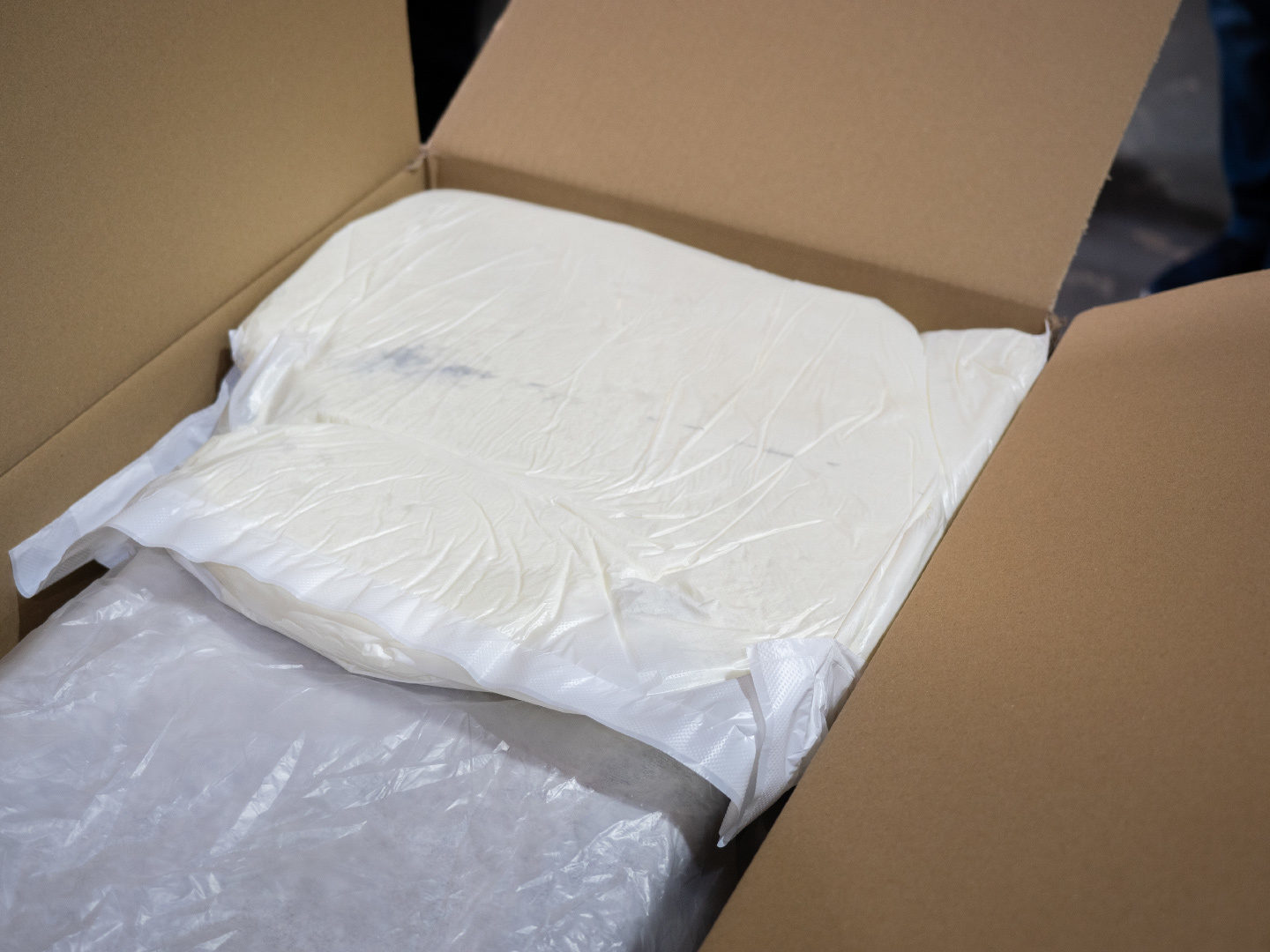
А дальше все на склад, и потом к покупателям.


Собственно говоря, нюансами упаковки можно было бы и пренебречь, как и некоторыми другими чисто производственными моментами. Но кому-то это будет просто интересно, а кто-то, так же как и я, оценит технологические и производственные подходы и внимание к деталям. В остальном, надеюсь, что фотографии все сказали сами за себя.